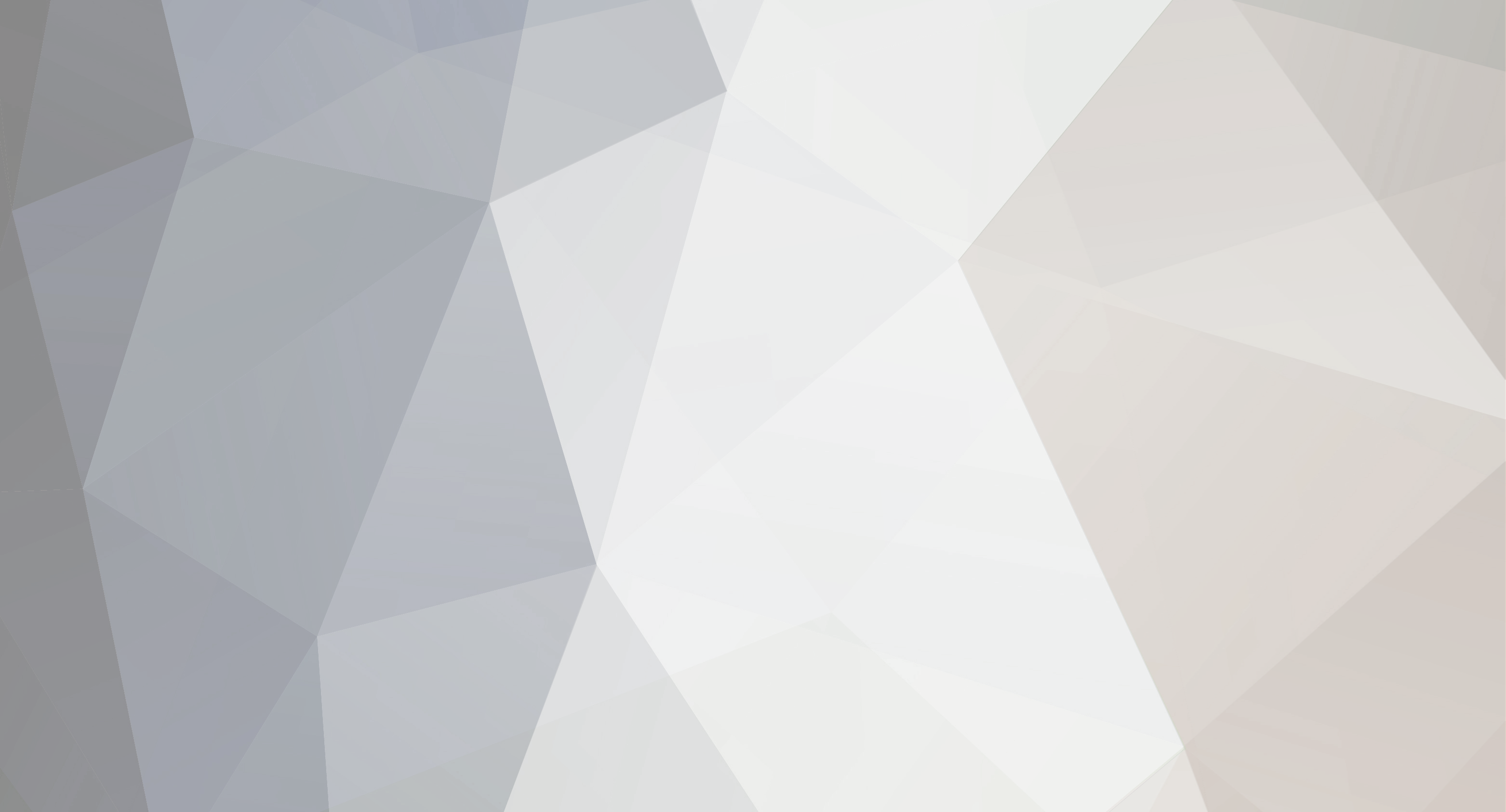
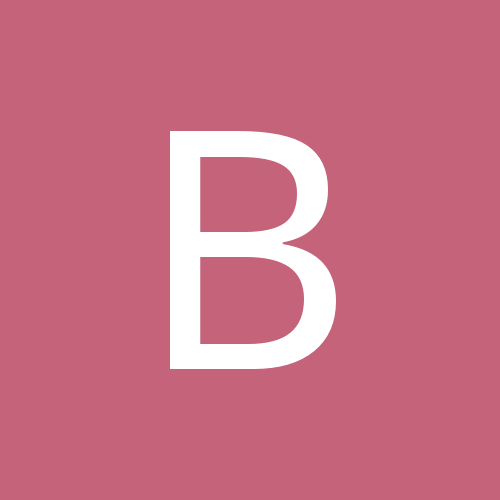
Brandiland
Members-
Content Count
18 -
Joined
-
Last visited
Content Type
Profiles
Forums
Gallery
Everything posted by Brandiland
-
Best Substrate for large indoor sign?
Brandiland replied to Brandiland's topic in General discussion
Thanks for the response everyone. I purchased some Gator board late last night. Some of the other substrates would have worked, had it been tan, but I read a TON of reviews on the Gator board. Seems to do what I need, and can last. -
I'm making a 30" x 36" sign that lists the companies dry rubs and marinades. This will be indoor, but I don't want it to look cheap. Any suggestions? Also, it needs to be tan. I was thinking of going with a foam board, but wanted to see if there was something better I could try.
-
Looking to buy the wax paper backing vinyl comes on by the roll.
Brandiland replied to redrub04's topic in General Help
Hmm, I ordered the wax paper from the site posted. There is no way I can use this stuff for decals. It's extremely thin and decals won't stick to it, at all. Does anyone know where to order actual vinyl backing? In the meantime, anyone need some super thin sheets of wax paper? -
Looking to buy the wax paper backing vinyl comes on by the roll.
Brandiland replied to redrub04's topic in General Help
Thank you for the info Slice. I tend to keep large sheets that are leftover as well. Of course, now I don't have any when I need it. I think I'll buy a roll and do as you said, and staple the edges. -
Looking to buy the wax paper backing vinyl comes on by the roll.
Brandiland replied to redrub04's topic in General Help
I saw the link above for the parchment paper. Can someone chime in, who has used it? I was wondering if the transfer tape sticks well enough to it,to ship. I'm currently cutting decals, and the client would also like the inside portion of the design, that I would normally weed out and throw away. Or, If anyone happens to know where to purchase the same mil wax backing,that would be helpful too. -
Alright, so I've dug around on here for a while. I can't seem to find what I'm looking for, but I've seen quite a few intelligent people, so I figured I'd start here. I'm using Signcut Pro with ARMS on a Saga 2400 cutter. I've read the instructions they give on how to align my registration marks. I even made my own registration marks at 25mm long in each direction (as suggested). I'm not sure my cutter is trying to see those marks. It's not consistent in its errors, making it very difficult to find the problem. Sometimes, when I click "ok" to cut, nothing happens. Sometimes, it trails off to the left and up as if it's looking for the registration marks, but then stops short, and begins the cut, or draw,in my case. I feel like I'm missing something. Can someone who uses the ARMS system with Signcut Pro help me?
-
<blockquote class='ipsBlockquote'data-author="Mz SKEETER" data-cid="412830" data-time="1455299864"><p> Are you putting the laser correctly inside the first registration mark, lower right> then setting Origin, then Click OK to cut.? If your doing all of that, then contact your support..techs. Signcut or Saga.</p></blockquote> Yep, did all of that. I emailed support yesterday. Hopefully, I'll hear something soon. I'm not sure how to add a picture, or I'd show you what it looks like.
-
What cuases this?
Brandiland replied to storm2313's topic in TITAN 2 Series Vinyl Cutter Discussions
I set the blade depth by taking it out of the holder, and cutting a circle on vinyl. The circle cuts through the vinyl, but just barely leaves a mark on the wax paper underneath. I place it back in the machine, and adjust pressure accordingly. I had a machine before this one, that cut fine. How do I add to the over cut? I'm not sure I understand that statement. Also, this test cut is from the machine, not the software, if that makes a difference. -
What cuases this?
Brandiland replied to storm2313's topic in TITAN 2 Series Vinyl Cutter Discussions
I'm having the same problem getting my test cut to align properly. I was hoping to hear it was a blade issue, or something similar. This machine is brand new.Just got it yesterday. Sigh, looks like I'll be making a phone call. -
Titan 2 Not Working and Flashing Blue Light
Brandiland replied to Brandiland's topic in TITAN 2 Series Vinyl Cutter Discussions
I spoke with someone from US Cutter. They told me my warranty is voided if I have to send the unit back, because I no longer have the box (box was damaged in shipping). So they are sending a motherboard when they get their next shipment of them, in about a month. I'm dead in the water until then. Even then, that may not be the problem, resulting in a longer wait, or worse..a dead machine. I'm a little frustrated about the box ordeal. I see on the site where you can be reliable for damages if not packed correctly, and it's damaged, but to not even get to send it back at all, just seems a bit much. I package electronics all the time. I'm well aware of the grade of box this machine requires. -
Titan 2 Not Working and Flashing Blue Light
Brandiland posted a topic in TITAN 2 Series Vinyl Cutter Discussions
Hi,I've searched the site, and can't find what I'm looking for. Please forgive me if this has already been mentioned. I have a Titan 2 refurb. I've been using it for about 9 months with no issues. Today,I turned it on and the cutting unit slung as far to the right as it could possibly go. Then, the display screen started flashing blue about every 2 seconds or so. I've turned it off and unplugged it When I turn it back on, nothing happens other than the blue flashing light. Please Help -
Titan 2 Not Working and Flashing Blue Light
Brandiland replied to Brandiland's topic in TITAN 2 Series Vinyl Cutter Discussions
Can you describe what the switch looks like? Or if that's the only thing like that inside the machine. I'm mechanically inclined, and have no problem looking inside. I just don't, in any way, want to void the warranty. Also, the display shows nothing.It just flashes about every2 seconds. Did your display do that as well? -
Titan 2 Not Working and Flashing Blue Light
Brandiland replied to Brandiland's topic in TITAN 2 Series Vinyl Cutter Discussions
Not the first time. I did eventually move it (while it was unplugged). Absolutely nothing happens when I turn it on, except the blue light flashing. It doesn't try to move, adjust, recenter..nothing. -
This is my problem too. Did anyone help with this?
-
I'm cutting a wheel decal that will fit inside the rim of a motorcycle.I know I'll need to allow for the curve, when calculating my measurements, but I'm a little unsure where to start.The rim is 17". I made this one that's attached, but it's straight. I'd like my clients to not have to work so hard to get the perfect fit. Any help would be greatly appreciated.