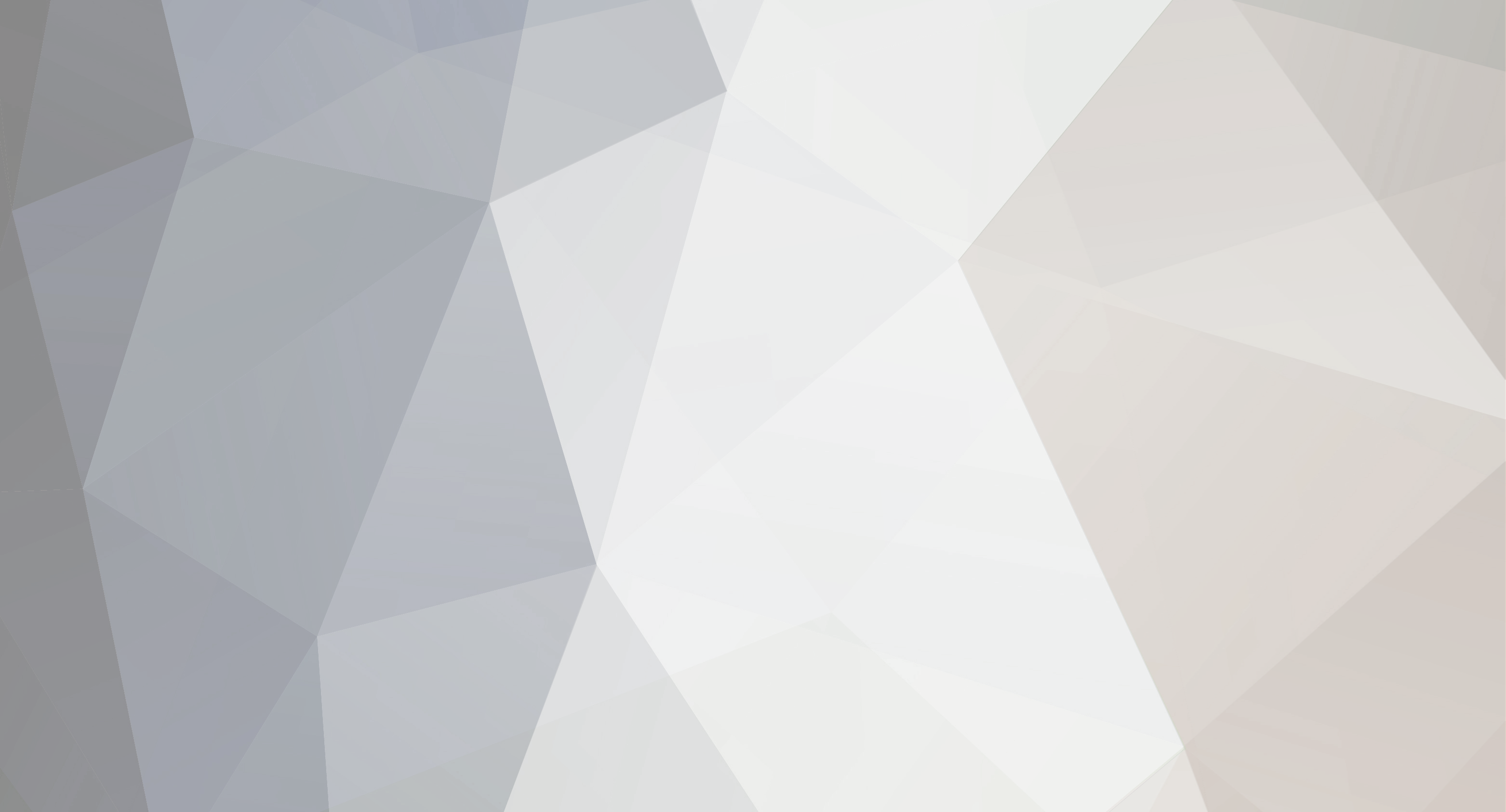
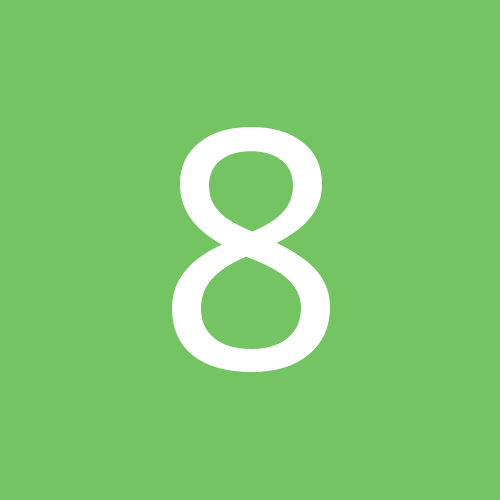
88x
-
Content Count
77 -
Joined
-
Last visited
-
Days Won
5
Posts posted by 88x
-
-
Hey slice, I too have a LP2 and match you almost exactly on the 250g force to get a good cut. I also had the same issue with the 1:1 sizing the cutter was cutting smaller then what I had it set at in SCALP but found in the settings (but it escape me right now what setting it was I will look when I'm at home) but with some test cuts of squares I ended up setting it to +1.025 for the x and the y and now they are spot on
-
-
T.WOOD
check this thread out even has pics of what I was trying to explain
http://forum.uscutter.com/index.php?/topic/48515-registration-marks/
-
Yeah you can. When you design it make each layer in a different color, then when you go to cut, click the tab "cut by color" in the pop up screen that you get and deselect or select the color that you want to cut. Then layer away
-
Have you tried to spray paint them with the tail light tinting paint? The one set that I did came out in a matte finish
-
Did you activate the Sure Cuts A Lot Pro 3? You have to, or it will be in demo mode and cut like that
-
I wish I had a metal workbench so the dang things would just lay flat. That's the real trouble with them.I used the top of the chest style freezer to make them lay flat
-
Primal,
Most people on here won't judge you about overlooking something or a setting.
What did you find?
-
1
-
-
Kris,
I also have a LP2 (31.5") had a very similar issue when cutting larger files. I tried the drier sheet trick but that didn't always solve the problem. I bought a Keyspan adapter about 2 months ago, since then I haven't had another issue. It has defiantly paid for itself without wasting vinyl
Later Nick
-
1
-
-
Cal,
What I meant was to remove the grid after you have everything placed, to make it easier to see that there isn't any overlapping. On a side note there is a way to change the grid layout in the view drop down, but every time I try to change it I get a warning that SCALP stopped working. I guess I just got use to removing the grid to check overlapping etc.
-
Select your text (so it has the arrows around it)
(By the #1) Click on the color box and change the color of the stroke to what ever you would like then click ok
Another thing to try when you are arranging your objects to cut, remove the grid so the mat is completely white, seems a little less cluttered. (easier to see your objects)
Hope this helps
-
2
-
-
Danica Patrick?
-
I filled out the form around 11:30am one day the next morning at 8:00am a local 3M sales rep called me to verify what I was looking at and said he will get the samples out within the next few days
-
-
When I run into this I just go to file then to recent projects and open it that way not sure why it does that sometimes never messed with it any futher than that tho
-
-
Here is a site that can give some great ideas for fonts on race cars
-
3.60 is good here too
-
That sounds just like my problem......so did you have to pay to ship it back? And did you have the box that say's keep this box for shipping?? Because my clean freak husband (love him), but he threw that box outLOL The problem happened right when I opened it and set it up so I had the original box. They sent a return shipment label through UPS. Once I shipped it I had to call them back, they tracked the package to make sure it was on its way back to them, then they sent out the new cutter (before it arived back to them). It was painless after the fact of figuring out what the actual problem was.
-
Sorry very late to the party but I can finally add something to this great forum!! I had this exact same thing with my Laserpoint II when I bought it last April. It would cut the path but would not lift up between the letters. I called tech support and they walked me through some trouble shooting and found it was the motor that does the lifting of the blade. The tech people asked If I wanted to replace the parts myself or just get a complete replacement cutter I opted for the replacement cutter and have had no issues since. It sounds like these awesome people have already trouble shot it for you, but thought I would add my 2 cents
-
Thanks to wildgoose in another post I took his advice and traced the image and it turned out perfect!!
-
I need your help with this font please I have checked though all my fonts, tried what the font. But haven't hit on it exactly. Thanks in advance
-
Unbelievable thanks for the help!!!!!
-
What do you think the font is for Todd County?
Red & Black -- LPII forms the visual centerpiece of my sign shop
in LaserPoint Cutting Plotter Discussion
Posted
Hey slice I checked that setting and it was called "resolution" that I adjusted to get the size the same. I do use sure cuts alot pro version 3 and 4, both are the same.