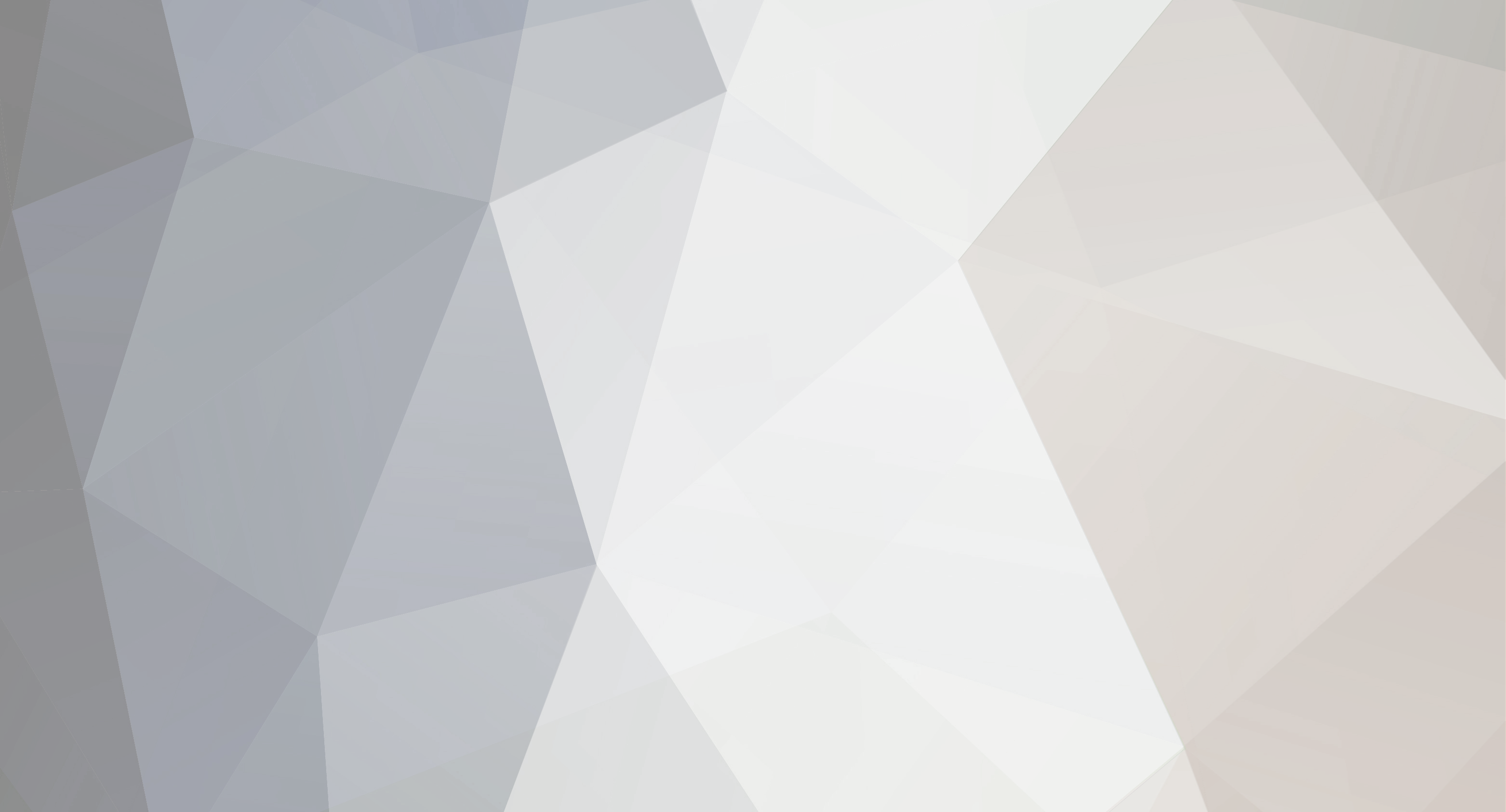

ShaneGreen
Members-
Content Count
188 -
Joined
-
Last visited
-
Days Won
9
ShaneGreen last won the day on December 9 2019
ShaneGreen had the most liked content!
Community Reputation
131 ExcellentAbout ShaneGreen
-
Rank
Advanced Member
Recent Profile Visitors
The recent visitors block is disabled and is not being shown to other users.
-
Mz Skeeter, I like that idea. May have to order one and see how thick the material is. Would still need to figure out a source for larger quantities.
-
ShaneGreen started following Shower Floor Material
-
Good Morning, Has anyone ever cut any non-slip material for a shower floor? Most of the pre-made stuff I find is PEVA or textured PET. But I'm not having any luck finding either of these in a cuttable roll or sheet. Can it even be done? They aren't wanting the sandpaper type material, which is a good thing since it would probably have to be die cut. The abrasives would chew up a blade in a hurry.
-
Laser point 3 wobble cut & more issues plz help
ShaneGreen replied to vixencharm's topic in LaserPoint Cutting Plotter Discussion
Is it just me, or does the jaggedness look very uniform? Like each little arc is the same size and direction. Take a look at the letter "E" and the long, vertical portion is nearly straight, which would be when the carriage sits still and the vinyl is pulled. But then you look at the ends of the three legs of the "E", which should be the save situation as the long section, but instead it's 3 nearly identical jagged profiles. A loose carriage shouldn't produce identical jaggedness. The plotter is being told to cut that way. My guess would be the wrong plotter profile. -
Software Update Issue
ShaneGreen replied to Lisa P's Kreative T's's topic in VinylMaster CUT, LTR, PRO & DSR
Check that the Vinyl Spooler stil has the right "port type" selected in the "connection" tab. For some reason when I updated, mine switched from "Direct COM" to "Direct USB". I reset it, restarted the program and all's working fine now. -
US Cutter version on Windows 10
-
Mine updated just fine. VM Pro on a Win10.
-
In the "Shapes & Welding" tools there is "Punch out" which removes the shape of the item above from the item below (think paper punch). Or "Stamp" which does the opposite, removing the object below from the one above.
-
VM calls it "tiling".
-
Vinyl Master Cut doesn't Import Image
ShaneGreen replied to a topic in VinylMaster CUT, LTR, PRO & DSR
Darcshadow, I've had the same sort of thing but rather than missing nodes it was extra nodes on lower layers. Almost like a square was node A1, A2, A3 and A4. When a copy was made it became B1, B2, B3, B4 and then moved. But when VM or Explorer see it it's reading A1, A2, B3, A3, A4, so the middle of one side took off in a funky direction. Deleting all the extra layers and objects gave me back the original image. -
Vinyl Master Cut doesn't Import Image
ShaneGreen replied to a topic in VinylMaster CUT, LTR, PRO & DSR
I've got thousands of svg files and VMPro does occasionally choke on one. The same files usually don't look right in Windows Explorer either, so it's more than likely an oddly formatted file. On the rare occasion I get a bad one I open it up in Inkscape first. Sometimes it looks off in Inkscape too. I'll highlight all of the visible objects and move them to the front level and change their color and then resave. If that doesn't fix the problem, sometimes I'll grab those objects and move them to a new file. A lot of the time it's an issue of duplicate objects on multiple levels that makes VM go crosseyed. -
At 6'7" I wear a "3xl Tall." When I was Fire Chief we had a lot of folks on the department that needed 3XL-5XL. The local screen printing shop owners were close friends so we did a lot of experimenting. Found out we were wasting time doing multiple sized images for the front of shirts. Most people can't tell the difference and if you make it real big the person looks like a walking billboard. . . and not in a good way. The back of shirts was on a case-by-case basis. If it was a short but wide graphic then it sometimes needed to be made bigger on the backs of the larger shirts. This was especially true if it was arced. Arced text on the back kind of needs to almost touch the shoulder blades to look good and when you start looking at someone my size that's quite a bit wider then a normal XL. You also need to take the weight of all that vinyl or ink into consideration. The wider it gets, the more it wants to make the shirt sag. When you scale up, the thickness of every stroke gets larger too, so if you put a 14" wide graphic on the front of a shirt there is going to be a lot of sweating going on.
-
Glad you found a good solution! Be sure and post some pictures and a review when you get it in. Never know when that sort of information might be handy.
-
I can make one the right size based on length and width, but can't seem to figure it out by angle. >Side menu select "General Power Shapes" > Polygon > then drag one onto your page >switch to object mode? the single arrow in the upper left of the menu that lets you select an object. > select the polygon > your upper menu now shows the polygon tools > change "points" to 4 > next to the width and height turn off the padlock, turning off "proportional" > now you can manually stretch the polygon or enter your dimensions in the width and height
-
Love It! Love It! Love It!
-
My experience with die cutting is in the cardboard packaging industry. Their idea of "high volume" is probably a bit different than the vinyl business. One job I had them running was 5'x3' sheets loaded every 5 seconds: load a sheet of cardboard, stamp, slide the parts off the press and load another sheet. At over 100 parts per sheet, one guy was putting out 2,000/hour. Rolls were handled in one of two methods: 1) Flat Die: an arm unrolled and slid the material under the die, retracted, die cycled, repeat. This was great because you could start with a small die with one pattern or a larger die with multiple patterns. They could also gang jobs to get the most out of each cycle. 2) Roller Die: a continual operation where the material roll is fed in the side of the press, the die is on a roll that spins at the same rate as material feed. This is super high volume and I only saw it used on smaller parts where die only had a few patterns on it. Not sure how this would work without stretching the vinyl. I tell you all this so you get a feel for their "volume". But it was their sample lab that held my interest and might give you some ideas. They used air-over hydraulic presses like in an auto shop, only with high-speed cylinders. Almost all of their steel rule dies were handcut plywood with the rules inserted no matter what the projected volume was. Handcutting is fine for cardboard, but vinyl would need more precision, like you'd get if you laser cut the wood. The leather industry makes a lot of their dies with laser cut wood and steel rules. They use toggle presses, air-over hydraulic, ball-screw presses and some other interesting machines. They are looking at tolerances a lot tighter and require quite a bit of force. They might be a good place to look. Depending on your tolerances and volume, you might be able to get going relatively inexpensively. There are folks on etsy making custom dies for leather and paper.