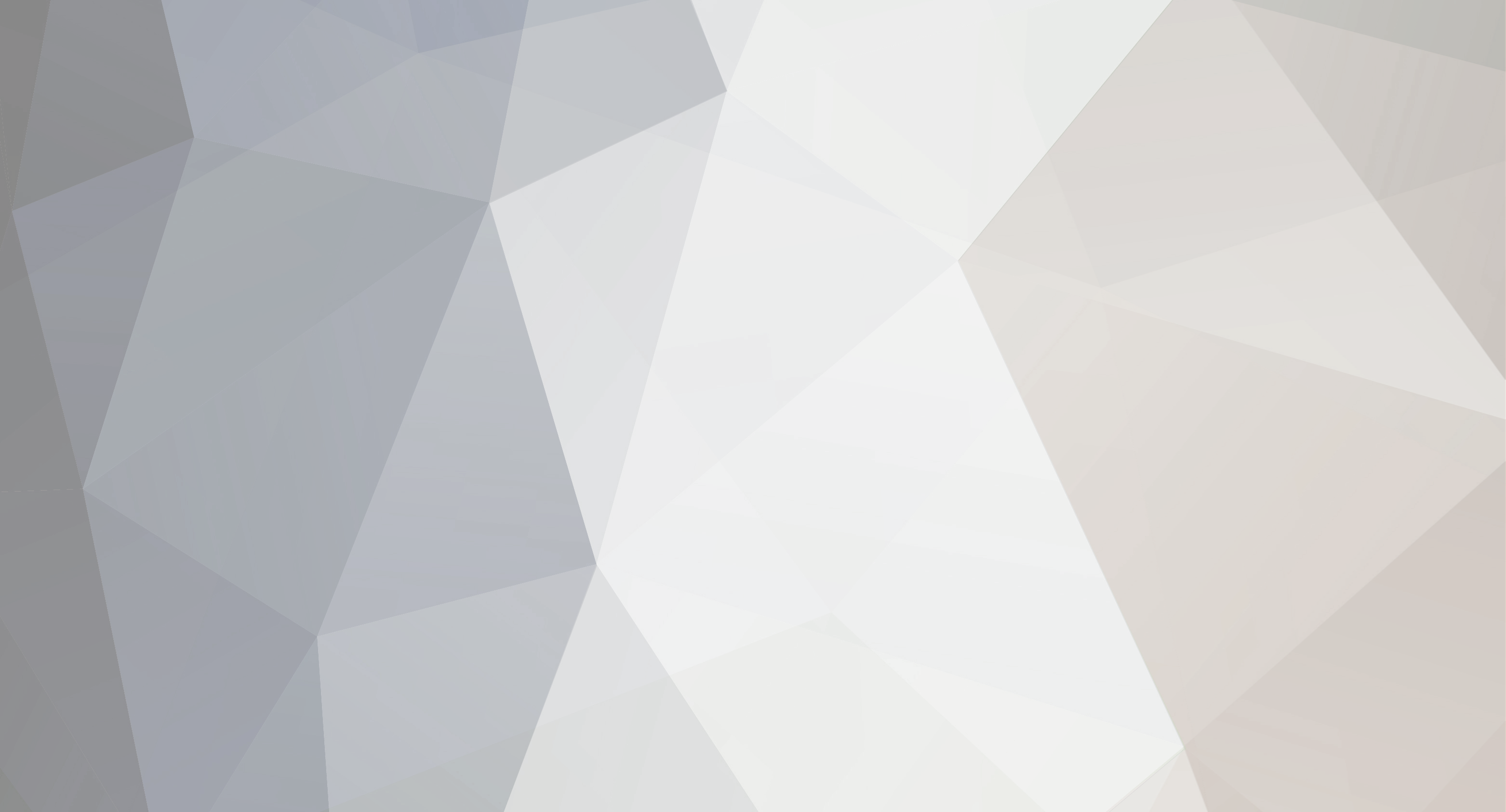
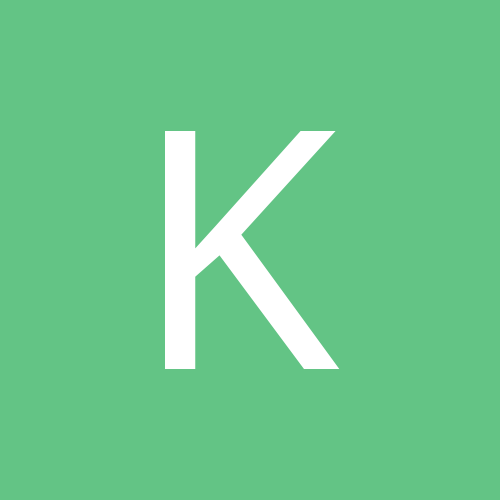
killerdecals
-
Content Count
26 -
Joined
-
Last visited
Never
Posts posted by killerdecals
-
-
have you tried setting your cutter up on a different com port than com1?,,, try 3, or 4.... Com 1 is usually used for an actual serial port connection. See if that helps. this is from the support section for USB, You did not state how you are connected. I am only assuming USB, Also I have been using Flexistarter for 4 years and love it. VERY ez to use. You might want to consider learning it. I have also included the info for serial port, try it on com2
USB
If you need to install your cutter through the USB port, you will need to install the USB drivers. USB drivers are available on our support site under Downloads, then MH/Refine Series Downloads. The USB driver is the very top selection, simply click on it and run it. It will self-install and when finished tell you that "FTDI drivers have been successfully installed." Once the drivers are installed, you can plug your USB cable in to the computer and Windows should tell you that "new hardware is found" and then "your hardware is installed and ready to use." You then need to check your device manager under the ports category to see which COM port the USB installed to (usually COM3 or COM4). Once you find out which port it installed to, you can then tell SignBlazer which port it is using and select the correct Device.
Serial Port (9pin cable)
Simply connect the cable to your computer from the cutter and set the SignBlazer software to cut/ plot through the COM1 port. If that does not work, you may need to try COM2 if you have had other devices hooked up to the serial port in the past.
Actually I am connected serial port but I have tried usb and changing com's as well and same thing. I am almost starting to think it is a cutter issue because signblazer is so simple I can't imagine it being that. This summer it got damaged by lightening during a storm because it was plugged in so I had to replace the motherboard and I/O board in it. I don't see why that would matter either but I am out of ideas here lol. Anyone know of a good site to learn how to use flexistarter?
-
Zoomed in and it isn't trying to tile their is only 1 box.
-
-
-
Nobody has any suggestions? Man this sucks lol
-
Might help you to list the cutter you have, the software you are using, and maybe even post the file for others to have a look at.
Fill out your Signature with the basic info like mine is done and then everyone knows what your using. And you won't have to type it out with each post./
Sorry I have the US CUTTER REFINE MH 1351 and I am using signblazer right now. I have flexistarter 8.5 but I have yet to learn how to use it so I continue with signblazer until then. As for the file it doesn't matter what I use infact I can just make a rectangle and it will do the same thing. Thanks
-
I am trying to cut racing stripes for a customer which measure 20" wide by 72" long. Now when I go to cut this and the machine prefeeds it should move across the vinyl very slow compaired to the rollers because it is only supposed to move 20" but instead it moves just as fast as the rollers and will not stop moving across the vinyl infact if will move all the way across the machine until it hits the otherside of the machine if you let it. Now if I make the length 65" or shorter it is just fine and works great but any length over 65" it will do this crap. Why would my length be making my cutter do this when it's the width that the cutter is supposed to be measuring across? Any help would be great thanks
-
That would only matter for more then one copies correct? It's not even checked for one copy. ThanksIn the cutter screen make sure the x,y values are small or your borders will be off
-
I have no weeding options checkeduncheck all your weeding options
-
lol yes this is a made up number thanks
It's just a customers phone number so I am not going to put a customers phone number on here. I have my work area set to 24" tall by 96" long and the 11 digit number 1-715-625-4785and the number size is 12" high by 90" long. This should be an easy cut but for some reason it doesn't like the length. I tried it at 5" and no problems but longer it does not like.maybe put up some screen shots of your layout screen before sending to cut, we cannot see what you are doing , just by you saying so.. Show it..
Just to make sure ...Is that a fictious # or the # you did not want to put on here ? I'll delete this post if it is the actual # .
-
yes I make sure the Origin is set. Their is no kill switch on the other side so it will move all the way across until it hits the other side then starts making a horrific noise then starts coming back the other direction. Very weird why it does this. I don't understand why normal lengths are fine but does this with longer lengths. ThanksHave you made sure to set your Origin? If it's not set, the blade will want to move to to Origin point first before it starts any cuts. Happens after it gets to the other side of the cutter? Does it hit the red kill switch button?
-
I want to find out why this is doing this. It is only 12" high I shouldn't have to tile and piece it together it should be a pretty easy run for the machine.Don't cut it all at once, do half or a third at least you should be able to get it done.
-
With something this long and only a foot high the vinyl should be feeding much faster then the cutter head during the prefeed but the cutter head is moving almost just as fast so the cutter head is off the vinyl at about 40" of prefed vinyl. Is any of this making sense or am I being confusing? lol
I have them both at 15" by 120"it can affect it.. also static. does the CUTTING SIZE CORRECTIOn in set up match each other OUTPUT SIZE CORRECTION, measured size, expected size?
-
I have them both at 15" by 120"it can affect it.. also static. does the CUTTING SIZE CORRECTIOn in set up match each other OUTPUT SIZE CORRECTION, measured size, expected size?
-
does it matter if you use usb or serial for long cuts?
It's just a customers phone number so I am not going to put a customers phone number on here. I have my work area set to 24" tall by 96" long and the 11 digit number 1-715-625-4785 and the number size is 12" high by 90" long. This should be an easy cut but for some reason it doesn't like the length. I tried it at 5" and no problems but longer it does not like.maybe put up some screen shots of your layout screen before sending to cut, we cannot see what you are doing , just by you saying so.. Show it..
-
It's just a customers phone number so I am not going to put a customers phone number on here. I have my work area set to 24" tall by 96" long and the 11 digit number 1-715-625-4785 and the number size is 12" high by 90" long. This should be an easy cut but for some reason it doesn't like the length. I tried it at 5" and no problems but longer it does not like.maybe put up some screen shots of your layout screen before sending to cut, we cannot see what you are doing , just by you saying so.. Show it..
-
I am trying to cut a phone number 12" high by 90" long on 15" vinyl but when I go to cut and it starts to prefeed it keeps moving left right to the other side of the maching rather then stopping at 12". Any Ideas?
-
Ok I have the Refine MH1351 cutter and it has worked pretty good thus far. What is happening is I am trying to cut a phone number 12" high by 90" long on 15" vinyl. I line the cutter up to it's start position and when I go to cut it starts it's prefeed as normal but instead of stopping at 12" it just keeps going until it hits the otherside of the machine. It works fine with shorter lengths but longer stuff it has troubles. So why during prefeed on longer lengths does it not stop where it should? No I do not have the X and Y measurments backwards either. Thanks I use sign blazer
-
I bought it a couple months or so ago and have never used it and yes I do have the dongle and it is in the usb. Is my computer missing something to open it such as a special java or anything? I just don't understand why it closes right away.Have you had the software for awhile? or just buy it? does it have the dongle? did you put the dongle in a USB port in your computer?
-
I have Flexi starter 8.5 too but I can't get it to open. It starts to load and when it is done loading and ready to open it just closes right away. Any Ideas? thanksI use FlexiStarter 8.5 and mine never cuts the tile lines, it starts at first tile, cuts everything in it, then advances to the next tile than does every tile as 1 continous design, maybe you can show screen shots of the production manager as to what you have clicked, before you send to cut.
-
I am also having the same exact problem and I have only cut maybe 6 items so far. I sent a support ticket but no response yet. If it is my mother board I will be upset. New machine and a deadline on a reunion order.
Did you ever get your machine fixed then?
-
Well after they made sure the settings were all correct which I knew they were then it narrows down to 2 things it seems , the I/O board may be bad or the Motherboard. Are you still under warranty? I found going to the Us Cutter website under support and trying to get the live chat help was great cuz they can access your computer via internet and check your settings and such. It is very frustrating when your machine does not work and you are slammed with orders I know. Good Luck!
-
They were a great help! They were on the phone with me for an hour or so and he accessed my computer via internet and looked at everything. We narrowed it down to the motherboard since we replaced the I/o board and that wasn't it so they sent me a new motherboard overnight and that was it so we are back in business!! We had a bolt of lightning hit our shop and I think that fried it because it also knocked the hot water heater out as well. Thanks to all the helpful techs at Us Cutter! They say your machines are cheap but they do the job just fine for me thank you! Also thanks to all of you for helping me get this figured out and giving me advice.
-
They said it was my I/O board so I ordered it and had it shipped overnight and that still wasn't the problem! $75 down the drain Grrrrrr I am getting so frustrated!
Cutter will not cut longer then 65 inches
in USCutter Refine Cutting Plotter Discussion
Posted
Thanks Speed I need to check that out