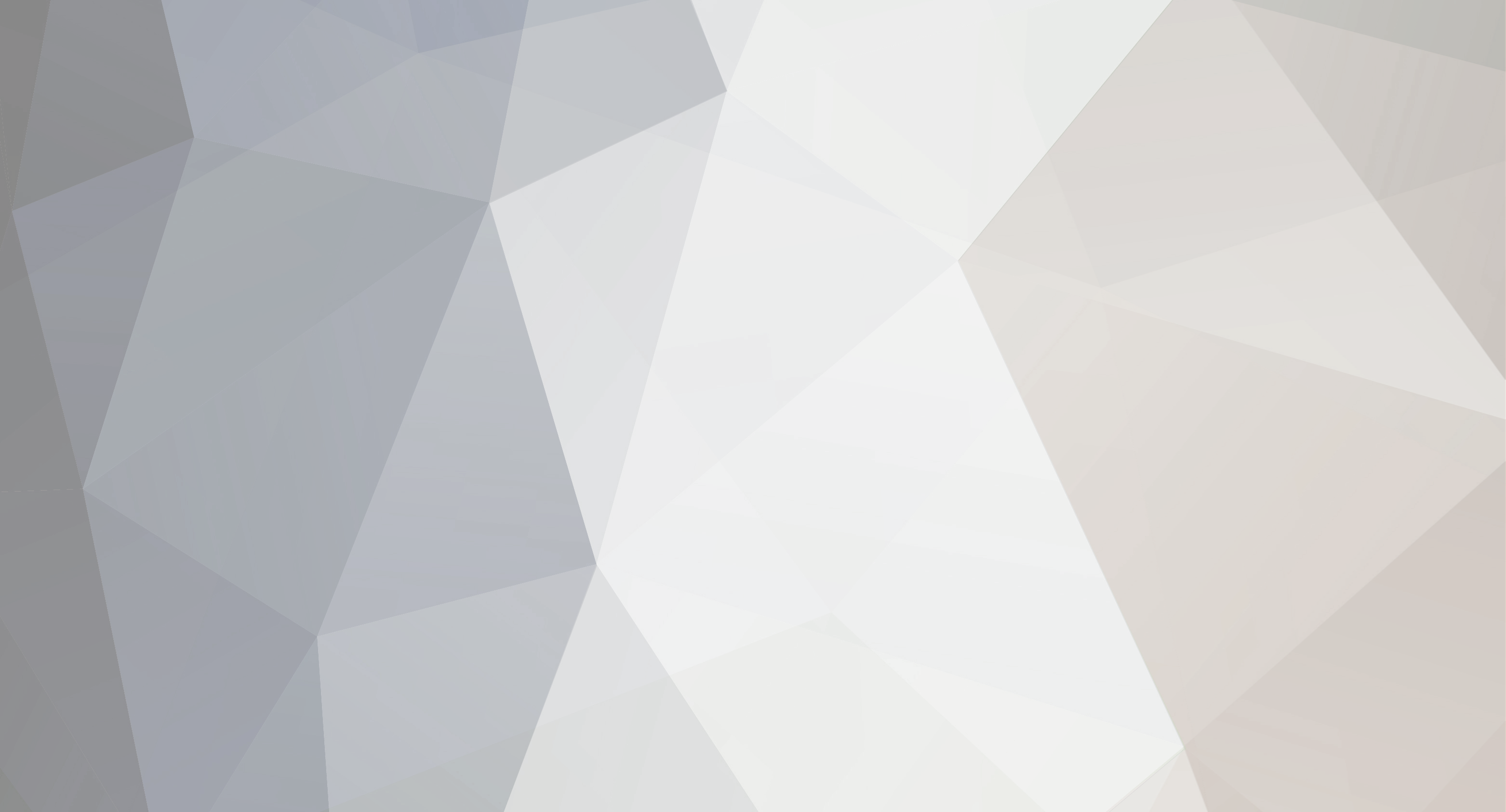
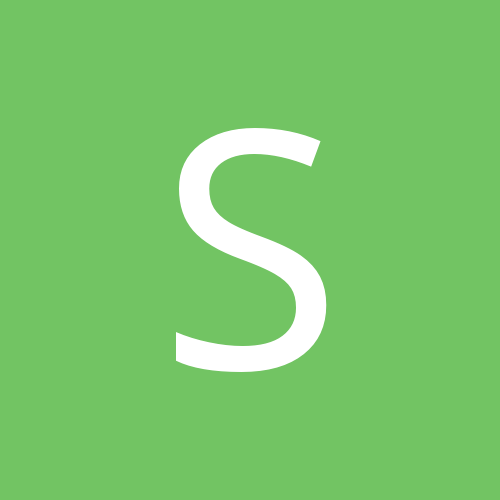
SignJunky
-
Content Count
123 -
Joined
-
Last visited
Posts posted by SignJunky
-
-
how did you make the buttons?
-
That's nice. Did you wrap around the outer edge of the tire cover too? My parents have an older camper and the end window cover looks pretty bad. It's some roughed up fiberglass. What kind of vinyl did you use on that? I was thinking about doing a lake scene since their camper is at a lake.
-
This is cool!!
-
Same wheelbase as hatchback. They just kept adding to the ass end til it looked like a clown car.You right..... so I guess I might see you driving it through the next parade? just kidding...... My boys would say..... " Put some rims on it and I'll drive it"
-
lol...... if it was about 15 feet shorter, it would look just like my mom's car 20 years ago!!! LOL.
-
convert your text to curves then send to me....... once you type the original text, weld then do your drop shadow. That process may be easier.
-
Just let me know. I'll help out if I can.
-
Send me want you have so far and I'll see if I can help out.
-
Vine Monogram is now popular also
-
I bought a training dvd - started from lesson 1 so I could fill in the gaps from where I was winging it - that was the hardest part as that is boring - but also picked up a few tidbits that make it worth it. Trying to learn the right way not the "I think I can do it this way" wayI know what you mean. I had gotten some videos on Corel when I first started and the beginning lessons suck, but you will be surprised on something small that you can learn. I will check out some learning stuff for PS later..... but right now " I think I can do it this way"
-
coaster I have been working on a photoshop one for a couple of months a couple of chapters at a time LOL - I think I still have 5-6 to go when I get time - this time of year that gets hard though - just replaced brake cable on fourtrax, split 1/2 of the wood I have that needed split then came in and did ordersI'm new to PS..... that's a very powerful program and it's just wild what can be done in it. Did you buys some videos or something??
-
it gets a lot worse before it gets better........ lots of more videos, reading, researching, videos, reading, researching, videos, reading, researching, videos, reading, researching, videos, reading, researching, videos, reading, researching,... and did I mention lots of videos, reading, researching......
-
Welcome to the forum.....
-
1
-
-
I would have at least sent my laundry with her - trading work that needs done!Yea, we see what kind of friend you are...... now lets see what kind of friend she is!
-
Very nice!!
-
Probably the same thing you done...... cursed without anybody hearing me. lol
-
and that is a good reason to have the all metal roland stand with the metal rollers so the vinyl can diappate the static to ground thru that means and not thru the cutter - vinyl and plastic table = troublethe stand will help with the tracking too. I don't use my cutter as much as I use to since I have the printer now, but tracking stinks with the cheap roll holder that it comes with. I will invest in an actual Roland stand one day.
-
Use a dryer sheet to rub the backing of the vinyl and the plastic on the cutter were the vinyl feeds in and comes out. I actually leave a dryer sheet right beside my cutter at all times now and never have a problem with static anymore.
-
The do not bend stamps are so the post office doesn't run the envelope through their sorter thing-a-ma-bob. I use regular white envelopes, 6x9, 9x12, 10x13, and shipping tubes...haven't had any complaints about decals getting wet, bent out of shape, or destroyed...but, I probably just jinxed myself...haha. I do get my share of customers saying they never received their decals...but I guess you've got to expect that from some dishonest people. I'm sure there are some that the USPS does lose, though.post office lose? It's funny to me that they "lose my decals" but never lose my bills. lol
-
1
-
-
my 77 pinto was the even rarer truck version - was a great st car.mustang . . . . here ya go
so, you would love to have a heat press and I would love to have your stang..... hmmmmm?
-
dinosaurs...... well, they are definitely extinct. I don't remember the last time I've seen one on the road.... or even beside the road since my moms.... lol
-
Nice!!!!
-
Roland with eco sol max ink here
-
hoping ot have the 65 out within a month or so - it is getting nice, jsut keeping too busy right nowhoping ot have the 65 out within a month or so - it is getting nice, jsut keeping too busy right nowI bought the 68 as a basket case and am slowly working on it as time allows. I couldn't of done a nice Mustang like I did this, the guilt would have haunted me. Finally got to my computer to post pic and they're all on my phone and it's on my dresser at the house so it'll have to be this evening.Jay
where the pics at?? lol
Pink Ribboned Out!
in Show your work
Posted
Wow..... Thanks for the info Jones!! I appreciate you taking them time to explain everything. That answers a lot of questions