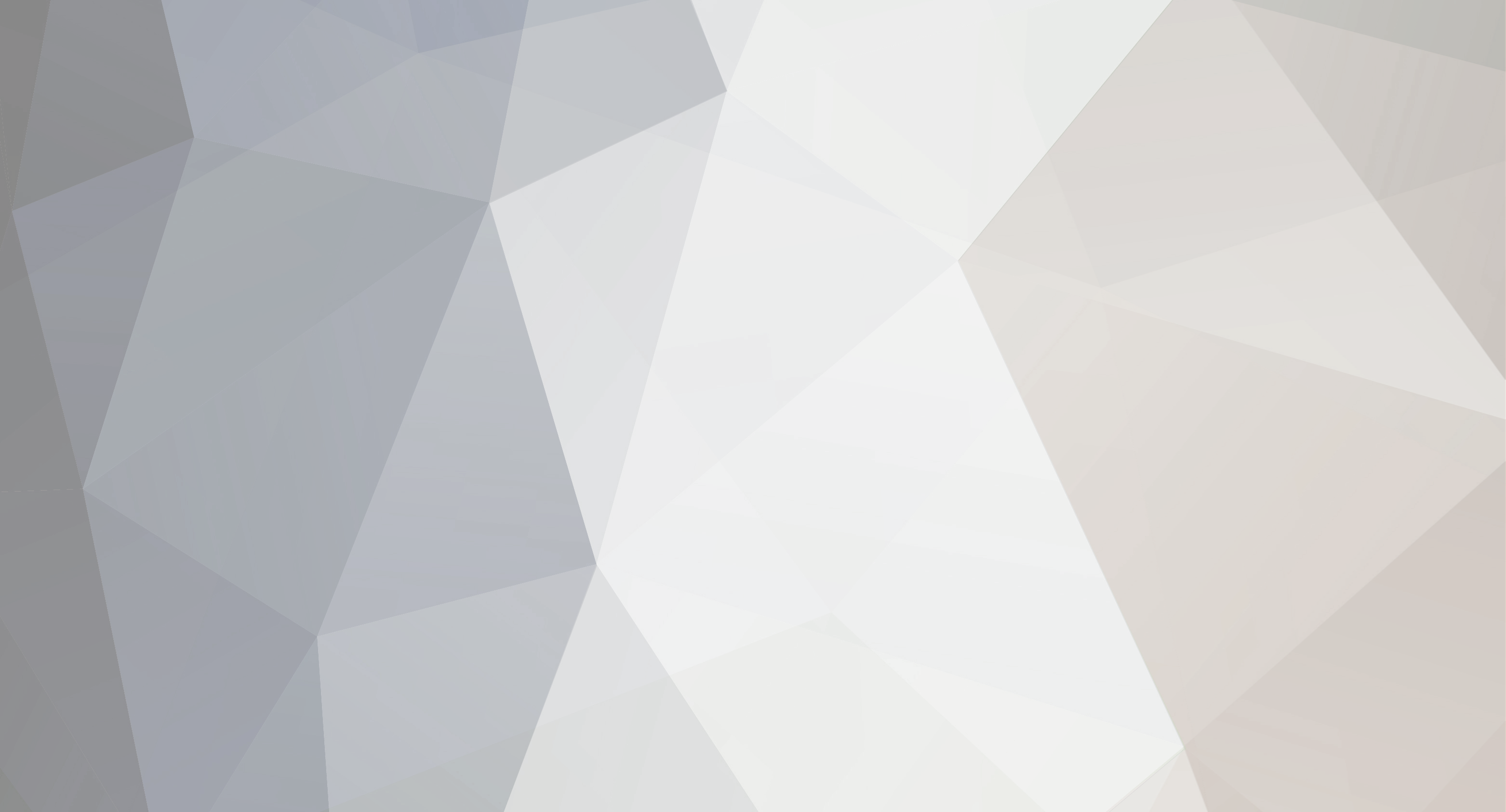
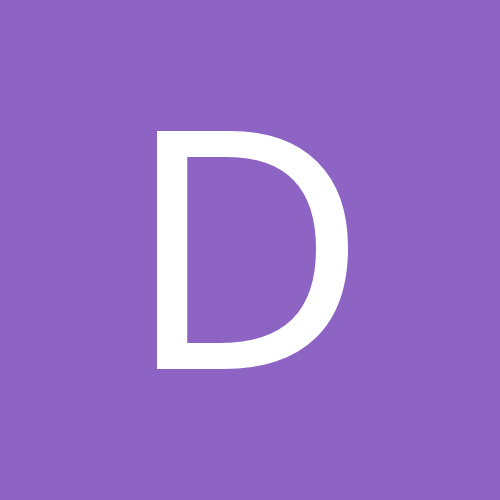
dbohemian
Members-
Content Count
10 -
Joined
-
Last visited
Community Reputation
0 NeutralAbout dbohemian
-
Rank
Member
- Birthday 01/01/1
Profile Information
-
Gender
Not Telling
-
Noobie having lots of trouble with Laserpoint 36 HELP
dbohemian replied to osrbikes's topic in Instructional Contributions
It should work....I don't know why you got the error you did when plugging in your USB. It's just that I have found and spent many an hour messing with laptop serial ports (or lack thereof) and then a small inexpensive desktop worked perfectly. I would not give up on it but if you can test it with a desktop and serial, it may be helpful. -
Noobie having lots of trouble with Laserpoint 36 HELP
dbohemian replied to osrbikes's topic in Instructional Contributions
I have a lot of experience with NC equipment (a plotter is just a simple 2 axis NC) and inevitably laptops have issues. Even when they have serial ports (older ones) I have had about a 50% success rate with them. Your experience is 100% opposite of mine. Desktop, plugged in to serial, loaded software and boom, cutting. I would first, find a desktop, it does not need to be fancy, can build a new one for 300 or use a buddies spare. Keep this computer for dedicated cutting. Blade installation and setting instructions are on this forum. -
Just bought US cutter MH 721 & need some help
dbohemian replied to Mudbug's topic in General discussion
Are you really using Windows ME?? ME was the worst op system ever by Microsoft are we talking an 8 year old computer at this point? I would say, use a serial port to test, ignore the USB right now. -
I understand where you are coming from, all valid points. But I see this as endemic across all business and this is why. You bought something that literally may have had a profit margin of 50 dollars, in some cases maybe a little more-little less. It used to be that when people lamented about the past and great service they had actually paid for it in the form of good profit margins. Now, there are no profit margins and when I purchased from this company, I read the fine print and figured I took a certain amount of risk along with the benefit of low price. If I wanted no risk, I could have purchased a more expensive unit that came with instructions, technical support, training etc. I am just playing devils advocate here, but heck you could have just purchased another one of these disposable things and had the returned one as a spare, they are that cheap. (I remember the old days when a mouse was 500 bucks) Service, costs money....That simple. Maybe yes, they should get more support and charge enough to hire this extra guy who will cost a fair amount to have employed, but then again the current business model is based predominately on price and value. My thoughts. Dave P.S. I had an issue BTW and turnaround on cases was just fine and the replacement part was sent ASAP, no charge. I am very happy. I also worked in tech support for a large US company and if you wanted more than 24hr response you had to pay extra for it.
-
NEW laser cutter but no laser light..
dbohemian replied to iwant2's topic in LaserPoint Cutting Plotter Support Requests
I think you should troubleshoot with Ken, but I will say that I had the same issue that you did recently with my new cutter. My repair, which may not be yours was to replace the laser. The connections where the laser was connected to power were improperly soldered. The laser, it turns out was just fine. If, this is the case with yours, I gave Ken a photo essay of what I did. It did require a few soldering tools, but I felt it much easier than returning a 50lb cutter that was working perfectly other than the laser for contouring which I haven't even started to do yet. Dave -
PCUT, SignBlazer and USB problem....
dbohemian replied to demondecals's topic in Creation PCUT Cutting Plotter Discussion
Many modern desktops do have a serial port but you may have to look on your motherboard and see if one is there. If it is than you could get a simple 3.00 serial port cable with a header for the back of your computer. I can only guess, but my guess is that the mobo of the plotter is pure serial with a USB device over the top and this is the cause of most of the issue (an inability to communicate) Serial is a solid interface. Since your computer is new I would for the moment rule out the plotter, and USB and run it directly with serial if possible. Troubleshoot from there. -
Free online pricing guides
dbohemian replied to firemalt's topic in Business Practices, Sales and Pricing, etc.
Yes, I would too, but it depends on your situation and overhead. What if you have a store front, employee, running the AC, health insurance, liability insurance, wear and tear on the machines and accounting for upgrades etc,etc, etc. That 40 might turn into 30,20,10 real quick depending on the situation. Just sayin -
Free online pricing guides
dbohemian replied to firemalt's topic in Business Practices, Sales and Pricing, etc.
So, I am not in this business, won't be in this business but I used the calculator to figure one banner 24*60 with high performance vinyl and it came to $88 dollars. Are you saying you routinely do it for $44.00 or less? I have purchased banners and never paid that little, nor do I see how you could make more than 20 bucks making a banner like that at 44 bucks. I could be wrong and I apologize upfront for that but the biggest problem most small business owners do to themselves is charge too little for their work when the market would bear much more. People go to pro's because they are skilled. I don't have time to shop around to save a 1.98 I just want the thing I want and I want it right. -
Hi Everyone, Newb here. Got a laserpoint. Cutting vinyl within minutes. No complaints at all. does anyone have a slick way of cutting the vinyl off straight without removing the material from the machine when you are done plotting? Is there some sort of gizmo that I can just lay the vinyl across and run a razor across it and bingo? thanks in advance. Dave
-
I am surprised. If vector magic does what you need it to do, quickly then it is a bargain for 2 bucks. Time is money....Spend an hour screwing around and you may have just lost all your profit.