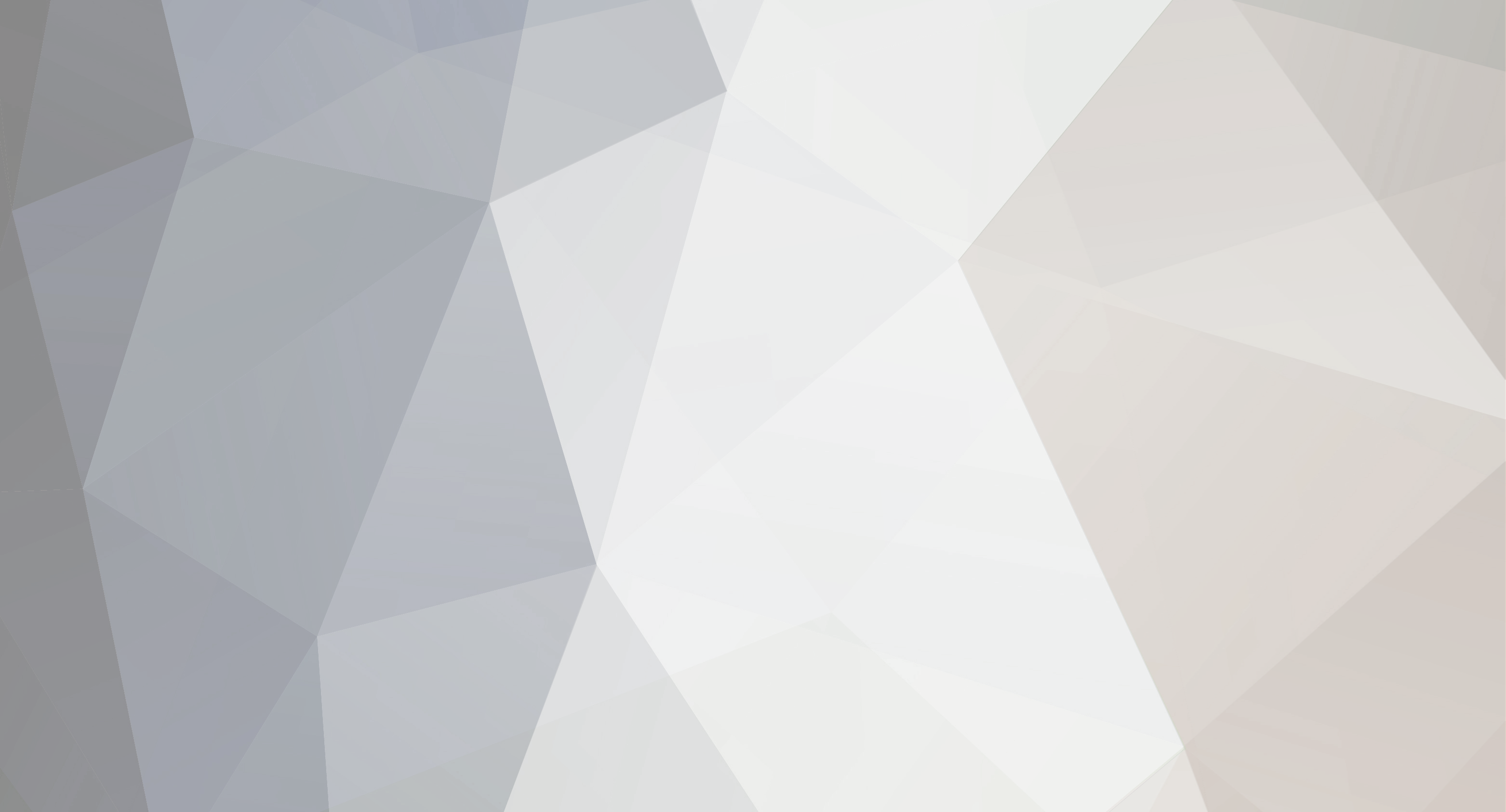
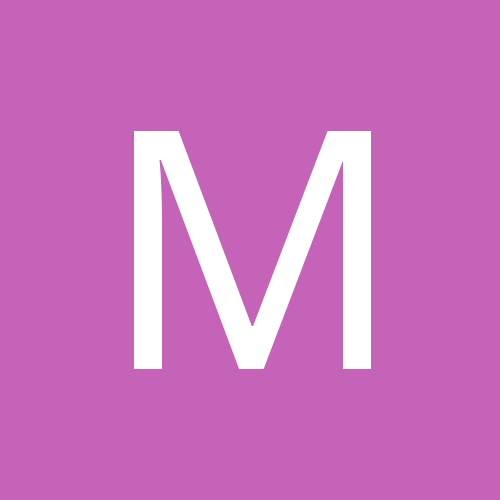
marcuso
-
Content Count
248 -
Joined
-
Last visited
-
Days Won
1
Posts posted by marcuso
-
-
Did you buy the machine from us? I don't have access to our orders database at the moment, but we haven't sold Artcut in a very long time. I have no love for the program.... We are probably going to start selling SignBlazer for $60-$70 if you are interested in better quality software. You can download a trial at:
-
Go with the Copam. Shipping costs are high to Mexico, so you might as well get the strongest, most reliable machine we offer.
-
We are interested in moving into other product categories. I would like to start a discussion about how our members see their business grow and progress.
What are the tools that USCutter can provide to help you take your business to the next level? I have found two product categories that I think may be a good fit for our business. One is laser engravers and the other is CNC machines. Are any of you interested? Do you think that it would add to the value of your business? Lets get a discussion going....
-
I honestly do not see a printer/cutter coming over the near horizon. There are only two manufacturers of such muchines, and they start in the $15,000 range. The worst part about it is that these printers are subsidized by over-priced ink, so realistically, the price is much higher.
What I do see as a possibility is a cutter that can contour cut using registration marks. Now, with that said, I would like to hear about peoples printing needs. For indoor printing, I think that the HP, Canon, Epson wide format machines that start at about $3000 are a great value. Of course, you pay an arm and a leg for ink with these. There is also the option of Encad Nova and the knockoffs. I have considered carrying these machines, and I think that I would be able to supply the really large models 60+ inches for about $1500. These would be models that aren't locked to a certain ink, so ink could be had for as low as $30 / liter. I don't know about the legality of selling these models in the US, but it would certainly be an option for those who are looking to print wide-format indoor graphics and then laminate (of course we would provide laminators too).
Of course, the aforementioned machines are of little use to those producing work for outdoors. To really take your business to the net level, you really need to go with a solvent type printer. I spent most of the last week looking at solvent printers and wondering if it was realistic for us to sell these via mail order without on-site service. I would like to hear your opinions. Is there a market for printers starting at $15,000? What are your printing needs?
-
It is unusual that you would have an LPT2 rather than LPT1. Try LPT1. Also, you should not have any printer drivers installed on the port (especially HP), so uninstall that and give it a try.
-
This was an open bug from Signcut that they say they have resolved. Download the newest version, and if you are still having an issue, let us know.
-
None of our current machines can read registration marks. We are looking at carrying machines that do in the future, so stay tuned.
-
I would say that 3mm is out of the question. 3/10 of a mm is quoted by the manufacturer. This refers to vinyl material. There are two main aspects that determine the maximum material thickness. First the blade. 60 degree blades are the standard for cutting thick material, and I would estimate that it is usefull for cutting no more than 2mm and probably less than that.
The other aspect (related to the cutter) is the strenght of the components. The motors must have the force necessary to slice through the thicker material with a blade that has less cutting edge (so it will need more pressure). Also, the carriage must have enough strenght to not flex under pressure. What we found is that the Refine cutter will flex under significant pressure. It can be partically compensated for with blade offset, but if you are looking to cut stencils, I would recommend the Copam. The PCUT would probably also be better than the Refine for stencil material, as it uses a stronger carriage mechanism, but we have not tried it yet.
Now, if anybody has any material that they would like tested, please feel free to send it in, and we will test it on whichever machines you would like.
- Marcus
-
I guess that I have sort of let the cat out of the bag on this one. For those of you who have been trying it out, you are free to discuss....
We are now bundling Signblazer, and for anybody that is not using Illustrator, Corel, or a Mac, I honestly think it is the way to go.
As far as the question regarding differences between our other models, I think the description is accurate. Parts quality and design of the PCUT are certainly of a higher caliber than the Refines. Our failure rate on the Refine models has been relatively high, and while I assumed that over time, the manufacturer would implement a quality improvement process, it seems that they are simply interesting in figuring out how to produce more machines. As such, I went out in search of a better product. The PCUT line while not perfect, is a very mature product and has a strong reputation. I always assumed that the pricing would be in the same ballpark as our Copam machines, but after probably 100+ hours of negotiating, we were able to get our pricing down to a reasonable level.... While still higher than the Refines, I would suggest that anybody considering a plotter purchase only chose between the PCUT or Copam.
Now with regard to the Copam, I am going to stick with what I have been saying all along. The Copam is THE MACHINE for professionals. It is much sturdier and heavier than ANY import plotter. It was engineer by Tiawanees rather than Chinese and quality was chosen over price. I am sure that anybody that is using a Copam will atest to this statement (please feel free to chime in)!
-
Are you using USB? Does it always happen in the same place? I have been at an industry show in China all week. One of the things that came up in discussions is that some Celeron processor motherboards have faulty USB chipsets. It was indicated that it might be related to current draw. First I would try using a serial port if you have one. Second, I would unplug all other USB devices and try again. If that does not work, try disabling virus protection and other non-essential programs.
-
The issue mentioned sounds like the sprocket / cog (whatever is on the end of the motor shaft) has come loose. Open up the side cover and see if that is the case. You can test by unplugging, and holding the the roller while you move the cog. If it is a bit loose, you can tighten it by removing the small belt and finding the hole. Inside, you should be able to tighten with an allen wrench. Let us know if this is indeed the issue.
- Marcus
-
Are those that are having problems using the USB adapter? What settings are you using? Are you using hardware flow control?
-
Good point and congratulations. You are now a global mod. Use the force wisely my friend.
-
aamotox,
What connection method are you using? If you are using USB, what settings are you using?
-
Our costs on eBay are higher than the website, so we would prefer to sell through the website.
-
You can cut pieces of vinyl to size for this cutter. My recommendation is to buy 24" rolls and cut 12"x24" pieces. These cutters are mostly used for making stickers. The 25" unit is far more versatile and usually worth the small price difference.
-
Beardown, I previously read that you have the blade sticking far out of the blade holder. Make sure that the knife tip is just barely out (enough to cut through just the vinyl without the backing). Use a new blade, and make sure that the blade rotates freely in the holder. Make sure that the blade holder is held tightly by the clamp. If it is still not closing cuts, set the offset much higher (if .032 is in inches, set it to .1 - that should overcut, but you can use it for testing). Let me know if that helps.
-
This could be an issue with the serial port baud setting. Do you have it set to "4800"?
-
What is your offset setting? (Try setting to 0 and see what it does....)
I am on a mac powerBook G4 and also an iBook G4, no intel and Mac OSX 10.4.9. the ploter is the copam. i am using signCut x2-PE and i have used both the USB/Serial Converter that was provided and i bought a Keyspan converter as well. the Keyspan was recomended by Apple Stores and Comp USA as well as the place that I downloaded the driver for the provided converter. with the original converter i couldn't get any communication to the plotter. i would send the file and no budge or anything from the plotter. sounds familliar with a lot of users. as soon as i used the Keyspan i got communication. a good sign but still having problems. i got some strange cuts that i couldn't figure out. look at attached files. i have so many questions and i am going nuts its been 3 long months of nothing and i am upset. here are my questions.
1.) i recieved a small disk with the plotter that my computer cannot read. it said it has drivers on it. my question is there a plotter driver or is there just the USB/Serial Drivers. if there is a printer/Plotter driver that i am not running let me know. willing to try anything.
2.) Am i running the corect sign cut for the mac I am using and the copam.
3.) I have turned down the baud to 4600 i believe (only 1 4500 or 4600). all the machine does after that is move the knife up and down and make a few noises, never cuts anything but after 20 minutes never does anything. thought i would wait at least that long to see if anything happened i have waited longer or just let it set ther but cant remember how long. but i change it back to the 9600 and i cuts but as you can see from the photos it cuts very strange. there is additional cuts insite the image as well as outside. it is as if it is trying to make a curved cut with many striat cuts as possible then it does random cuts as well. the photos of text are one long curve the srait lines are the plotters random the fonts are troy i think and zapfino if wondering. going by what i have told you where sould the baud be set? i also notice that somone had said that there is a setting on the plotter itself for changing the baud. if so where is it on the copam. Again willing to try anything.
4.)i have been to the Network settings and checked the port configurations to make sure they are on or checked and used correctly. they change acording to the USB port you use on you computer, if you have more than one usb port. and i do change them accordingly in signcut under device to the corect port used. as for the "Cutter" window what are the settings needed to run correctly. as per the hanshake and blade offset. etc. Also what sould be the correct settings for the "settings for cutting" window.
I am willing to do anything to get this plotter up an running. i just want to fix the problem and get going. please help. Anyone.
-
Yep, You are the first to point it out. I am trying eliminate the number of posts that are going to the wrong categories. I hope everybody is happy with the changes.
-
Here is the deal:
Up until today, we have been nothing but nice to this person. In addition, he has been leaving out a number of details.
To make a long story short, we have sent out a bunch of new parts. I am guessing that the original mainboard went bad in shipping. As the customer mentions, they didn't seem to understand how to hook up the power supply (and probably fried some of the parts in the process). The vinyl cutter was bought on eBay, so it only had a one month warranty, yet I agreed to keep on replacing parts under warranty. At no time (until now) did we insinuate that it was his fault for hooking it up incorrectly, we just kept on dealing with the customer in a professional, reliable manner.
As of about a week ago, my technician, Ken, started getting calls from Adam and Adam's mother making demands that they talk to me. I asked Ken what had happened, and he said that he had offered to replace parts once we received them or to send them out immediately if a deposit was placed (as per our standard policy for warranty covered parts). He also told me that he had been yelled at by the customer and had remained calm and nice the whole time (Ken is good at that). So, I called the mother and listened, and explained that this was an unusual circumstance, and I would take care of it right away. I told her that it was only a one month warranty and asked if it was within warranty. I even told her that I would send it out without a deposit if she promised to send the defective (or unused) parts back - I also agreed to pay for International priority shipping. I went and boxed up a new mainboard and LCD (just in case it was the LCD) and sent it out immediately. Unfortunately, I am not the one that handles these situations (Ken is), and since they chose not to talk to Ken anymore, he didn't handle it, so I sent out the wrong motherboard.
Ken talks to me today, and tells me that he has been getting calls from Adam and his mom again because I sent the wrong motherboard. Adam had said that the machine worked except the LCD was blank (would be resolved with correct mainboard), but he still wanted a new machine. Ken said that he offered to send out a whole new machine, but he needed the old unit or a deposit first. He said that the mom agreed to that, but then he got a call from Adam who started yelling at him, and insisted that he talked to me. At this point, I am frustrated, because Ken is doing his job correctly and having to deal with two people instead of just one, and I am not inclined to be nice to customers who yell at my employees.
So Adam got on the phone with me and started venting his complaints to me (in a very rude manner), and I asked him what we could do to resolve the issue. He told me that it was my responsibility to send him a new vinyl cutter, and he wasn't going to send the old one back first because he still needed it to complete work. I told him that if he wanted us to replace the unit, he would have to either put down a deposit or send the old one back (keep in mind that he wants us to send out a $950 vinyl cutter plus the $100+ in parts that we had already sent without receiving any payment). He insisted that this was not fair and started threating us by going to eBay and with legal action.
After he started threatening me, I told him that if he was going to continue threatening me, I would no longer help him. I don't expect that he or his mother will send back the parts that they promised, so I am no longer going to help them and I have instructed Ken to do the same. I don't want to waist our time any further. I will allow Ken to post a reply to this, and if the original poster (Mark or Adam?) does want to continue posting here, I will allow them as long as they keep it in this thread. If they start posting outside of this thread, I will block their account.
-
They were deleted because the quota on the board was originally set to a low value (10MB). I went ahead and increased the quota, so it should be a long time before attachments are deleted again.
-
Billy is right on this. We have been using two different backend softwares. Uscutterdirect.com and the uscutter ebay ID are run on the Zoovy e-commerce platform. Zoovy has been far from ideal, but we ran some auctions through just to see how well it would work in production. I have decided that I will probably switch to another solution, so we have stopped using Zoovy for eBay auctions. It is my intention to settle on one solution and run all auctions through one eBay ID in the future. Unfortunately, it is taking longer than I expected, and we are still working on it. So for the time being, all auctions are being run through the selltopia userid.
-
We new have the 48" unit in rather limited supply. The price is $1099.99 plus $150 S&H. We don't have it available on our website, but PM your phone number to me if you would like to purchase one.
Pre-Buy Question
in Introductions
Posted
You will receive a receipt and a Fedex tracking number. If we send express to Mexico, I think that you should receive it in less than a a week, and probably even quicker. You have no need to worry.