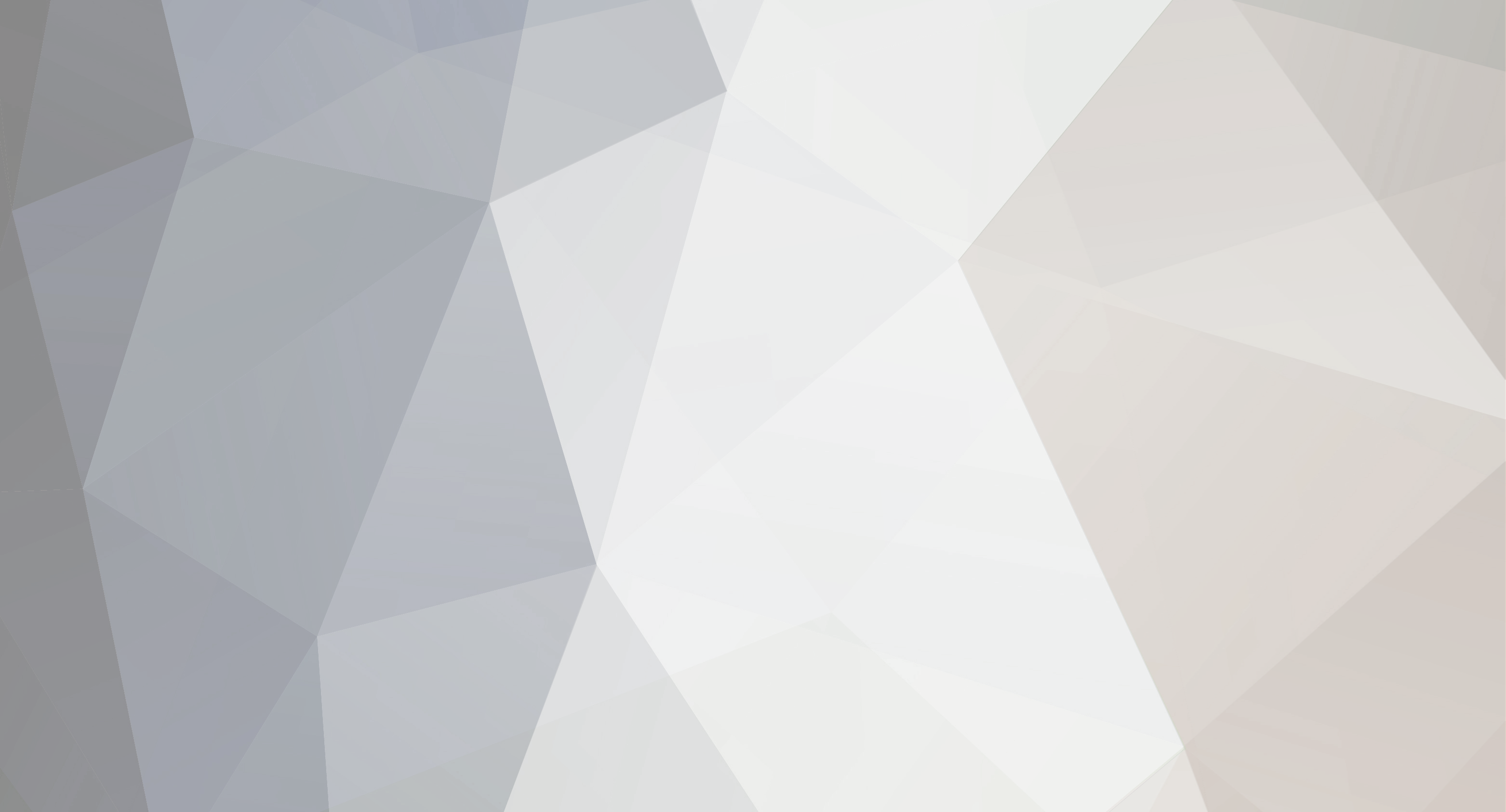
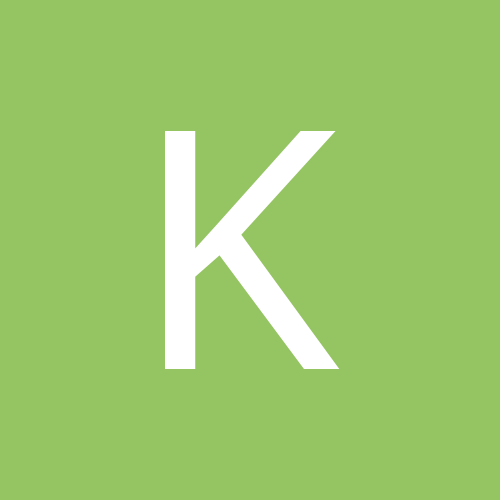
Kristof
-
Content Count
72 -
Joined
-
Last visited
Posts posted by Kristof
-
-
1 minute ago, MZ SKEETER said:I am with you on that one. I know what nesting is. LOL The same as in this industry.
I also have nothing to add to this thread either
You asked the question on why the material would be wasted, so I replied to you with a legitimate answer..
-
4 minutes ago, MZ SKEETER said:I don't see why you would need pre feed with sheets.
Probably because I don't want to cut the roll into sheets.
-
1 minute ago, MZ SKEETER said:How do you figure your going to loose over 11" of material per cutting?
It's called nesting in the industry; you can get more parts out of a single 24 ft long sheet than two 12 ft sheets, depending on the part dimensions.
If one part is 13 feet, neither sheet can be used and is why longer steel lengths are better (in this case magnet material).
-
1 minute ago, Dakotagrafx said:sounds like your margin isn't high enough to account for nominal waste . . .
The material is expensive and the market doesn't support high margins, just the way it is.
Honestly, the prefeed would function perfectly if there were more than two options. If it didn't have that ramp up acceleration it wouldn't trigger an error. I don't see why I can't set the pre feed speed in cm/s.
-
Cutting the material would be a waste of material for subsequent jobs where the cut line would've fell onto the next sheet, which potentially means a loss of 280mm of material. The roll should be kept continuous to not waste the material.
The geometry of the stock rollers is what causes unnecessary drag, they should be mounted up higher so that the material feeds in a planar manner and not angular (the departure angle of the roll).
Most jobs would be 560x560 but I may occasionally get odd ball jobs from customers that need to be 560mm in width by whatever length they specify.
Hopefully you understand..
-
57 minutes ago, Dakotagrafx said:more rollers I don't think will affect the weight of the material that causes the error
you could possibly set up a plastic table on the input and output side creating in effect a flatbed scenario - or just cutting you material in shorter lengths. just a suggestion
I was thinking that more rollers increases the amount of pulling weight and more traction, since the weight is spread out over four rollers. I already built a smooth melamine outfeed table that mounts to the stand and that turned out nice.
-
4 minutes ago, MZ SKEETER said:Then don't use the prefeed.
I wanted to utilize that feature. I think the media stocker rollers are mounted too low and the pulling angle creates drag that it has to fight against.
-
9 minutes ago, MZ SKEETER said:Where do you live? Besides East coast.
WV.
Do you think having more push rollers would stop the 'media too heavy' error from occurring when I do the pre feed? The error occurs even with the pre feed speed set to slow. It prefeeds fine at first and then as it accelerates it triggers the error; if there were a way to disable that acceleration/ramp up for pre feeding, that would solve my issue.
-
5 minutes ago, MZ SKEETER said:Maybe this is why. Stated on their ads.
Please Note: Additional Push Rollers must be installed by Graphtec or Graphtec Certified Installers.
There's not a dealer close to me.
-
1 hour ago, MZ SKEETER said:You have never stated, exactly what your doing, what condition, what force, ? But did you ever try the Tangential Emulation, which is for cutting thicker material?
As many of us stated. We do not cut magnet material with a vinyl cutter. This is entirely your experiment. We cannot answer your questions, or tell you what to do, because we don't do it. We will not put our cutters thru that. Most here cut sign vinyl, or some reflective, which they cut in passes. Graphtec is your tech support for your cutter. Craftedge is your tech support for your software.
https://www.youtube.com/results?search_query=Graphtec+FC8600+tangential
The force is currently at 28 and speed set at 2cm/s with acceleration of 1. I've heard that people have problems with tangential emulation, so I didn't think to try using that since it's not a true tangential machine and I don't think I need it, as all of the DXFs have corner radii and never sharp transition corners.
I uninstalled Sure Cuts a Lot since it's not very good software and am using the Illustrator and Cutting Master 4 plugin, which allows me to use the plotter on the network and is awesome! DXFs seem to be importing fine into Illustrator for now.
Still curious on how the push roller assemblies are installed so I can keep that as a last resort. None of the service manuals mention it.
-
1
-
-
Would it be a bad idea to cut the magnet with the 3M wax paper side facing the blade? I would get more traction with the grit rollers biting into the magnet material, but the swiveling blade may 'gum up' as it cuts through the 3M acrylic adhesive?
Just wondering. Thanks for your input!
-
The Graphtec service manual for the FC8000 doesn't even show how to change out the push roller assemblies.
-
I'm having trouble locating the post where someone installed the extra rollers; I could've swore I found it on other forum before while doing my initial research of plotters.
-
15 minutes ago, Wildgoose said:I think you would definitely benefit from the extra pinch rollers. I think I mentioned that I once considered an FC machine and they last who was the rep had a 30" model that had been set up to go to a sand blast outfit who would have been cutting blast resist which is similar in thickness to magnet. They had at least one extra roller maybe two and she said it was to help feed the material straight due to the heavy pressure of that thick a cut. I was going to pull them off for what I do and just save them for replacements or something.
Does it look hard to install/take off the rollers? The square bar looks like it runs through both sides of the machine and it looks like it needs to be taken out.
-
Is it pretty easy to install extra push rollers? I have a mechanical background.
-
I think I might benefit from installing two additional pinch rollers in the middle; $255 each though.
-
1
-
-
I tried the pre feed setting as well, and it causes the machine to report 'media too heavy' even if setting it on the Slow feed setting.
-
I guess it does work correctly depending on what you're doing. The blade goes up 5mm (as I want) at the end of a cut job. If the blade is down when powering up the machine and then jogging, it won't go up though, which is what I'd like.
-
So, I set the blade up height setting to 5mm to prevent dragging, but the blade doesnt go up to this setting before I jog, which can cause some faint scratches on the media.
I'm guessing there's not a setting to keep the blade always up in this 'parked' position until I initiate a cut job.
-
16 minutes ago, MZ SKEETER said:That cutter does have Pre feed on it. Pre feed and back. It pre feeds many, many feet. I looked at mine and got to 90 ft.
Does it put all the pre feed material in the media basket? The magnet would stick to itself.
-
I think I lost traction because I didn't pull enough off of the roll accidentally.
Is there an external roller stand available to where I can mount on the wall high up and pull off let's say 7 ft (height of wall) at a time?
-
Unfortunately, with the liner side facing down, I lost traction and the second pass was way off from the first one
-
-
4 minutes ago, MZ SKEETER said:Your showing UNITS as inches in your settings from what I see. I thought you used Metric. And you can change the steps resolution. Calibrate the cutter to the software. Nothing more I can help with SCALP. I was given a demo to try. I didn't like it all. I use Flexi software.
Yes, I changed that to be 25.4mm, but when I reopen it, it reverts back to displaying Inches.
Help!! Magnet cutting, machine hard to calibrate
in TITAN 2 Series Vinyl Cutter Discussions
Posted
Thank you, Sue! I am grateful for the wealth of posts that were posted here. I guess I have not explained myself well enough and people don't understand what I want