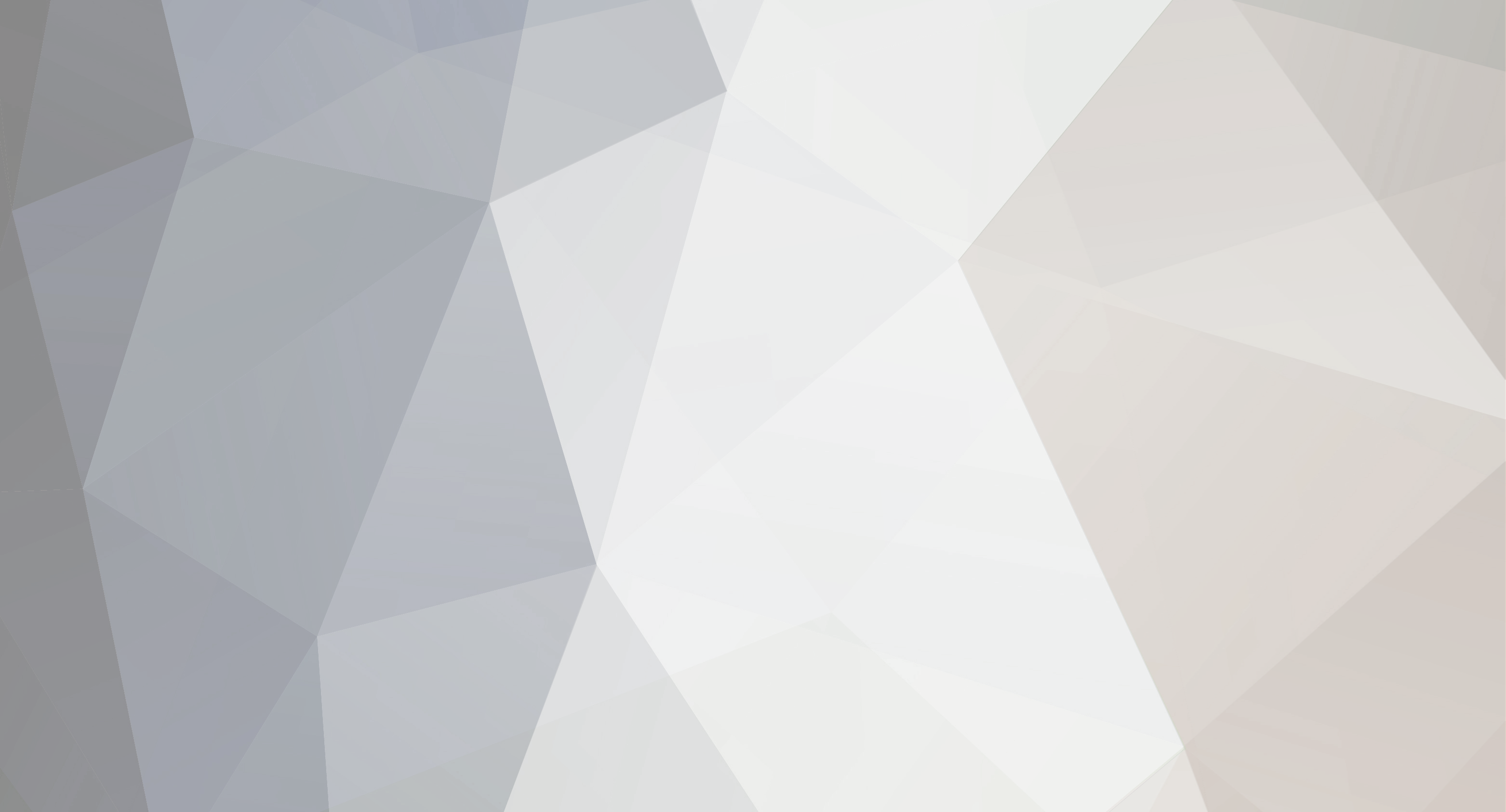
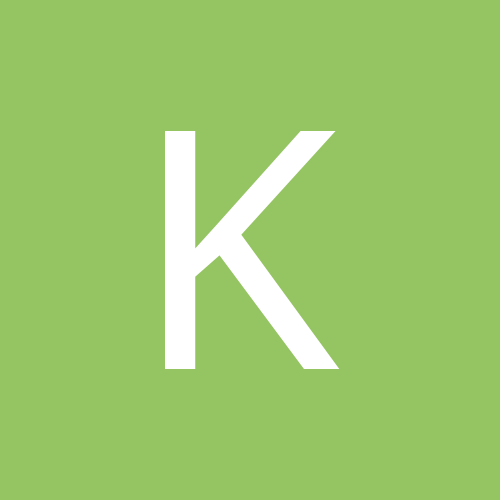
Kristof
Members-
Content Count
72 -
Joined
-
Last visited
Content Type
Profiles
Forums
Gallery
Everything posted by Kristof
-
Help!! Magnet cutting, machine hard to calibrate
Kristof replied to Kristof's topic in TITAN 2 Series Vinyl Cutter Discussions
Are you located far away from the east coast? -
Help!! Magnet cutting, machine hard to calibrate
Kristof replied to Kristof's topic in TITAN 2 Series Vinyl Cutter Discussions
The Graphtec FC8600 video on youtube claims it can cut up to 60 mil material and lists 'sandblast rubber material' as a media type. -
Help!! Magnet cutting, machine hard to calibrate
Kristof replied to Kristof's topic in TITAN 2 Series Vinyl Cutter Discussions
You don't think the 24" 8600 will work for my needs? -
Help!! Magnet cutting, machine hard to calibrate
Kristof replied to Kristof's topic in TITAN 2 Series Vinyl Cutter Discussions
I'm kind of in a pinch, I have no qualms about purchasing the 24" model FC8600, but if I have issues with cutting magnet with it still I feel like I would've wasted time and could've got one of the $3-5K chinese flatbed cutters with vacuum hold down. -
Help!! Magnet cutting, machine hard to calibrate
Kristof replied to Kristof's topic in TITAN 2 Series Vinyl Cutter Discussions
Up to 560mm in length and width for the biggest pieces I'll be selling, or 560mm in diameter for circular shapes. Also, ideally, I would like to not cut the rolled material so I can maximise 'nesting'. The material is extremely costly, so I would like to be able to manually pull some off of the roll but have it still be connected/non cut. The machine will be dedicated for only magnet cutting. -
Help!! Magnet cutting, machine hard to calibrate
Kristof replied to Kristof's topic in TITAN 2 Series Vinyl Cutter Discussions
USA, east coast. I understand that. I found this one post that mentions that the FC series can be problematic with cutting magnet material: https://signs101.com/threads/cutting-magnet-on-graphtec-fc-8600-anyone-try-it.130436/#post-1275924 -
Help!! Magnet cutting, machine hard to calibrate
Kristof replied to Kristof's topic in TITAN 2 Series Vinyl Cutter Discussions
I can't seem to locate used ones, do you have any good links? Otherwise, I'm willing to buy a brand new one. Couldn't I send the magnet material to someone to test though? -
Help!! Magnet cutting, machine hard to calibrate
Kristof replied to Kristof's topic in TITAN 2 Series Vinyl Cutter Discussions
Also willing to send it to someone with a laser cutter. -
Help!! Magnet cutting, machine hard to calibrate
Kristof replied to Kristof's topic in TITAN 2 Series Vinyl Cutter Discussions
I'm willing to send some of my magnet material to someone with a Graphtec FC to confirm if it will work or not. And to confirm, you don't mean the flatbed Graphtec FC cutters? -
Help!! Magnet cutting, machine hard to calibrate
Kristof replied to Kristof's topic in TITAN 2 Series Vinyl Cutter Discussions
It is a special type of magnet material compared to the traditional fridge magnet material; it's made from Nitrile and can withstand temperatures to 150 ºC. I'm going to try getting an RMA for the plotter. On a side note, I'm impressed with how well the CleanCut blades work on this magnet material. -
Help!! Magnet cutting, machine hard to calibrate
Kristof replied to Kristof's topic in TITAN 2 Series Vinyl Cutter Discussions
Of course not. Any laser should have fume extraction, however. The magnet does have an adhesive liner/carrier sheet, so it doesn't need to be cut all the way through unless you mean something else? The problem with not cutting it most of the way through is it leaves the edges rough when you break the magnet free compared to the carbide blade cut edge. -
Help!! Magnet cutting, machine hard to calibrate
Kristof replied to Kristof's topic in TITAN 2 Series Vinyl Cutter Discussions
I did actually; I played with the blade depth, downforce, tried three and four passes, and tried cutting the magnet with the wax paper liner side facing down. No dice. Calibration is inconsistent. -
Help!! Magnet cutting, machine hard to calibrate
Kristof replied to Kristof's topic in TITAN 2 Series Vinyl Cutter Discussions
I need to cut circles and custom shapes though, so I doubt those would work. -
Help!! Magnet cutting, machine hard to calibrate
Kristof replied to Kristof's topic in TITAN 2 Series Vinyl Cutter Discussions
What should I buy then? I can't seem to locate the manual wall mounted slicers that are used for glass cutting in picture frame stores, etc. I don't think we can afford a flatbed cutter; what other alternatives can I use? We have to cut circles, etc. -
Help!! Magnet cutting, machine hard to calibrate
Kristof replied to Kristof's topic in TITAN 2 Series Vinyl Cutter Discussions
The salesman said he wouldn't recommend cutting material over 45 mil with it. He also said I would get a hassle-free money back if I had any issues. -
Help!! Magnet cutting, machine hard to calibrate
Kristof replied to Kristof's topic in TITAN 2 Series Vinyl Cutter Discussions
My apologies if it sounded like I wasn't taking advice or haven't tried to search before posting. I am definitely going to try multiple passes! As a machine designer, I was merely curious how the plotter actually advances the depth of the blade on each pass. From my prior knowledge, I think this can only be accomplished with a leadscrew and motor. -
Help!! Magnet cutting, machine hard to calibrate
Kristof replied to Kristof's topic in TITAN 2 Series Vinyl Cutter Discussions
I have not found anyone who has asked the same thing that I have posted. Most posts for help on this forum don't include the detail of information I provided, because I have read a large amount on the forum before feeling the need to register as to not waste anyone's time. I guess no one in this thread can answer my technical question about how the cutting holder actually works. Short of taking the blue cover off of the carriage, I thought an expert on here would know. -
Help!! Magnet cutting, machine hard to calibrate
Kristof replied to Kristof's topic in TITAN 2 Series Vinyl Cutter Discussions
What do you mean by good luck? 30 mil is within the capabilities as was told by the salesman and why they recommended a servo drive. Again, it doesn't seem like my question was answered: how exactly does the solenoid control the depth on each subsequent pass? From my understanding, a solenoid is either fully up or fully down? -
Help!! Magnet cutting, machine hard to calibrate
Kristof replied to Kristof's topic in TITAN 2 Series Vinyl Cutter Discussions
I don't understand what you're saying? I asked a question asking how the multiple passes physically works? If the blade is either fully down or fully up, how exactly does multiple passes work? If the blade advances let's say 200 microns down each pass, this would be understandable to me as it's taking less of a 'bite' of the material per pass and is how other types of machines with a Z axis work. (CNC background) Sorry if I sounded confusing -
Help!! Magnet cutting, machine hard to calibrate
Kristof replied to Kristof's topic in TITAN 2 Series Vinyl Cutter Discussions
I still don't understand what 'multiple passes' means if the bladeholder solenoid is either fully up or fully down. The pinch rollers are also fully covering the material, cut and not-cut. I'm also not fully cutting through the material either. -
Help!! Magnet cutting, machine hard to calibrate
Kristof replied to Kristof's topic in TITAN 2 Series Vinyl Cutter Discussions
How does multiple passes work exactly? Does the solenoid somehow increase the depth on each subsequent pass? Otherwise, I don't understand how this works. I will gladly try multiple passes if you can explain how the feature works. The magnet material is loaded into the plotter with the 3M kraft paper (adhesive liner) facing up due to the way the magnet material is rolled. -
Help!! Magnet cutting, machine hard to calibrate
Kristof replied to Kristof's topic in TITAN 2 Series Vinyl Cutter Discussions
I am not understanding how the amount of passes would correct the dimensions and the non square cuts that I am trying to solve? Can you enlighten me? Thank you so much for helping!