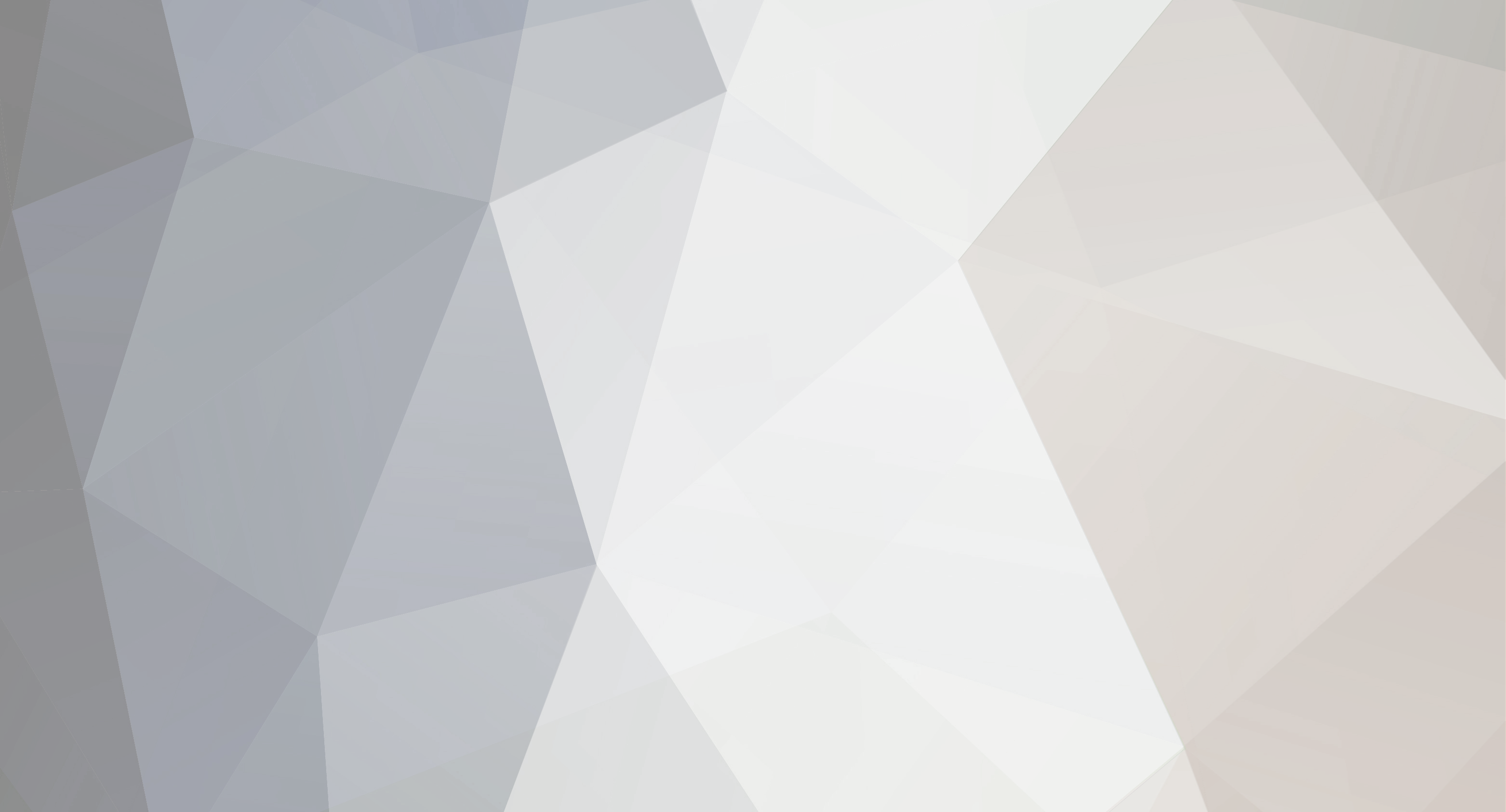
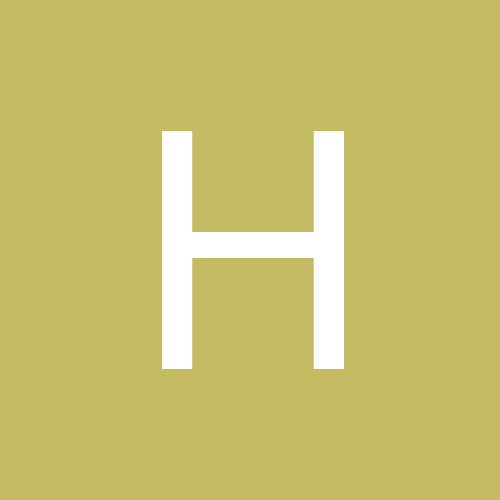
hockeygirl
Members-
Content Count
617 -
Joined
-
Last visited
Content Type
Profiles
Forums
Gallery
Everything posted by hockeygirl
-
I am trying to cut a whole row of the same design (2.5"x10"), so 8 of them with weeding frame on a 24" roll from signcut pro (I have MH721 with usb if that matters - serial port does not work at all, so please don't ask me to try that). The cutter cuts the first 2 (closest to origin) then does an incomplete cut of the 3rd. It then proceeded to jump to the far end of the vinyl and started cutting the last sticker (8th), the one previous to that (7th) and again, does an incomplete cut on the 6th, and then it goes back and try to cut the 7th one again. That's when I hit the reset button. I tried it again and it did the same thing (although the level of cut non-completion on the 3rd and the 6th stickers varies). So, 2 tries and I can only get 4 good stickers out of the width of the vinyl (a bit of a waste, isn't it?) So... if anyone can think of what's going on, or what I can do to fix the problem... the machine is properly grounded and there doesn't seem to be static-related issues, I have done plenty of cuts like this, but this is the first time it behaves this way... Thanks in advanced!
-
I would email SignCut with all the registration info at support@sc-x2.com. If you need to use SignCut in a pinch, download another copy and register with a different email address to get a new temp registration code, while they resolve the original problem. They can always transfer the code you got when you purchase the cutter to the new one to extend your 1 year. Or you can also try their "Live Support" at http://www.signcutpro.com/support.html
-
How much in profits is reasonable ?
hockeygirl replied to jibr's topic in Business Practices, Sales and Pricing, etc.
We do a lot of smaller order screenprintings (anything over 100 shirts, we outsource). T-shirt costs about $1.70 each wholesale and we typically charge a $25 screen fee. But all material costs to do per shirt is under $2. We charge $12 per shirt for single color and each additional color would cost them an extra $25 screen fee + $3 per shirt. We found it to be a lot more efficient and profitable than doing vinyl for T-shirts (ink is cheap)! So, if we're doing an order of 50 shirts, that's $12x50+$25=$625. Our cost (assuming we already have the screen, if not, that's $15 for the screen): $2x50=$100. Being super conservative, it takes maybe 2 hours including setup time to do the job, labor cost: $45/hr x 2 = $90. Profit = $625-$100-$90-$15(screen) = $420 for 50 single color shirts. Of course, higher quality shirts costs more... this price is for Guidan Ultra Cotton T-shirt. So, even if we do it at $7 per shirt, we're still looking at $145 pure profit (and it really doesn't take 2 hours to do them). BTW, the prices you can charge also depends on your location as well. We operate out of California, living expenses are high and we're able to charge more if they want the shirts printed locally instead of online. -
Want Reliable Clear Tape? My Review on TransferRite 1510
hockeygirl replied to john!'s topic in Instructional Contributions
I do a lot of stickers to sell, those look better on display with clear tape over paper tape... Personally, I prefer the RTape over TransferRite. I use the AT60 Clear Choice for standard stickers and AT42 RLA Clear Conform for the bigger or highly detailed ones. -
Hi, after being the 3rd owner of a 6-yr old MH-721, it's finally giving me more problems than I want to deal with... So, I'm looking to replace the cutter with either an identical model or the PCUT. What's your opinion on the PCUT? I read from the description that only USB is available, is it reliable or is it as flakey as the USB on the Refine? The COM port or the Parallel port on my Refine never worked ever since I took it over, the previous owner said the COM port worked for awhile before crapping out and he had to use USB after that. Also, does the Refine stand work on the PCUT? So I might save some money not having to get the stand if I go with PCUT... I'm open to any and all suggestions. Thanks!
-
Thanks for all the responses! If the new Refine are quieter, that may lean my decision towards it a bit... Another question I have on the PCUT, I know it advances after the cut, but do you have the manually take it offline and reset the origin like you do with the Refine? I have to do that with my Refine every time, even after SignCut advances the vinyl after the cut. Otherwise, if I forget to manually reset the origin, for the next cut, it'll go back to the previous origin and I would've screwed up the vinyl...
-
Won't Complete Frame Cut
hockeygirl replied to skylineracer's topic in USCutter Refine Cutting Plotter Support Requests
Are you talking about the weeding box in SignCut Pro? If you're only cutting 1 copy of the design, SignCut Pro doesn't cut the final side of the box. I never saw this problem with SignCut-X2 but the first day I switched over to Pro... Now that you mention it, I submitted a ticket to SignCut back in May but don't remember hearing back about it. It wasn't a big deal for me, I kinda just "ignored" the issue. -
Cannot cut large files on MH721 & Signcut
hockeygirl posted a topic in USCutter Refine Cutting Plotter Support Requests
Hi, I know this had been posted multiple times, but none of the fixes posted seem to be working for me.... I'm using MH721, direct USB connection - I cannot use Serial as the plotter does not communicate with my computer at all, and have tried this on 2 different computers. Everything is fine when I'm cutting smaller designs, but the bigger ones (larger than 2'x2'), the plotter stops in the middle of the cut and it seems to have lost the USB connection. I cannot restart the plotter unless I physically disconnect and reconnect the USB cable. I had been using Signcut-X2, switched to Signcut Pro and the same problem still exists. The problem is also a little random, because when that happens, I just exit the program, restart it, and it will almost always cut the entire design this time around. I'm a little annoyed because I'm also wasting a lot of vinyl because of this. Any suggestions? Cutter is approx 3 years old. Here are my settings in Signcut Pro: Manufactuere: USCutter Cutter: USCutter Refine MH721 Output Device: USB Serial Port (COM4) Baud: 9600 Parity: NON Databits: 8 Stopbits: 1 Handshake: Hardware Any ideas? Thanks and appreciate any help.... -
Cannot cut large files on MH721 & Signcut
hockeygirl replied to hockeygirl's topic in USCutter Refine Cutting Plotter Support Requests
Sorry for the delayed reply, I was on vacation the last couple of weeks. Finally back to reality... Thanks for the suggestions, the cutter is already grounded, but I will try taping the cable down and see if it makes a difference. But it is an older machine and components may be getting worn so I'm not really complaining much. And I have found ways around large files by splitting it into several smaller files and do my best to match it up(tedious, but it gets the work done since I'm in no shape to invest in a new machine)... and I just hold off on large intricate designs these days.