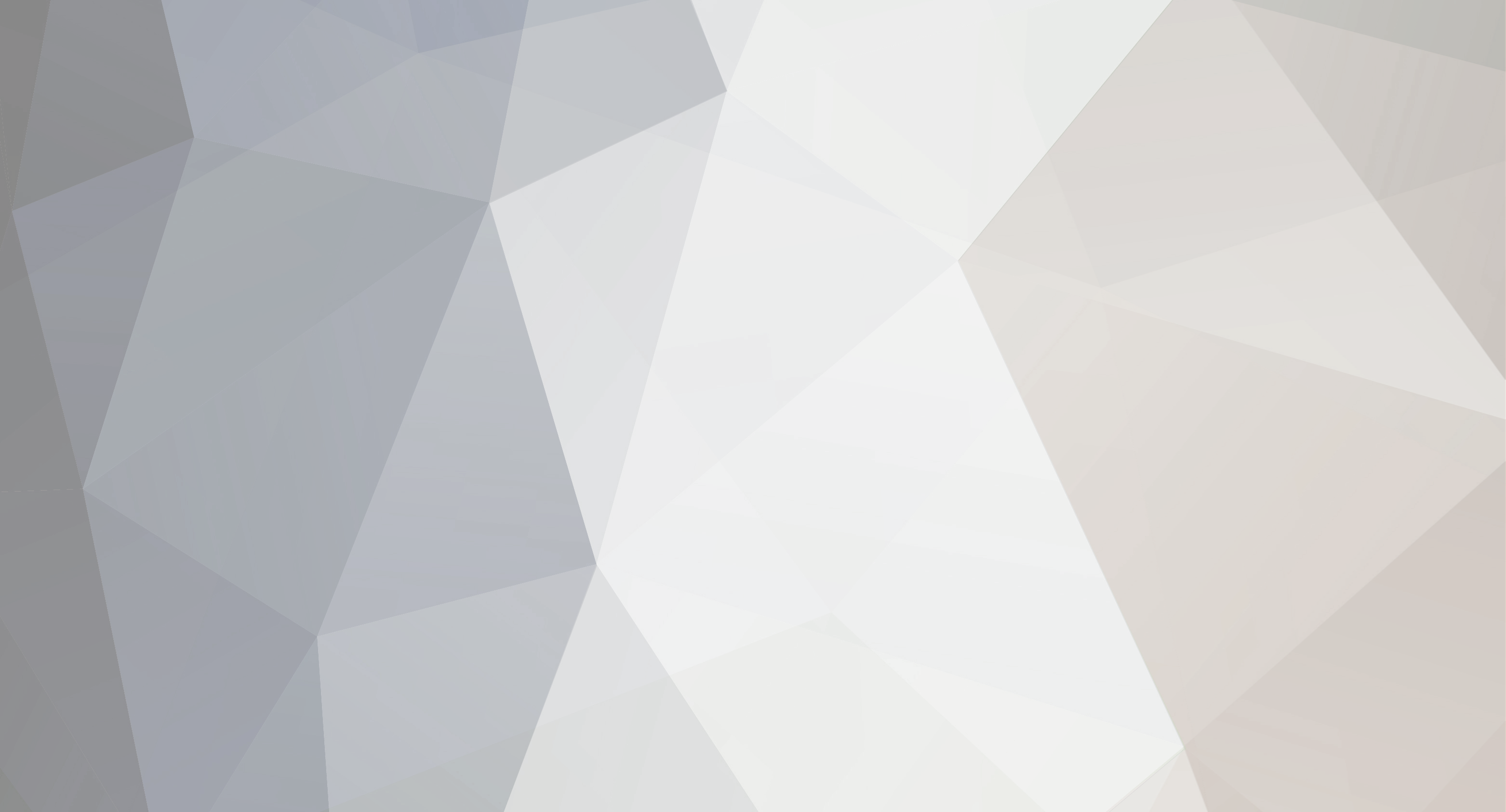
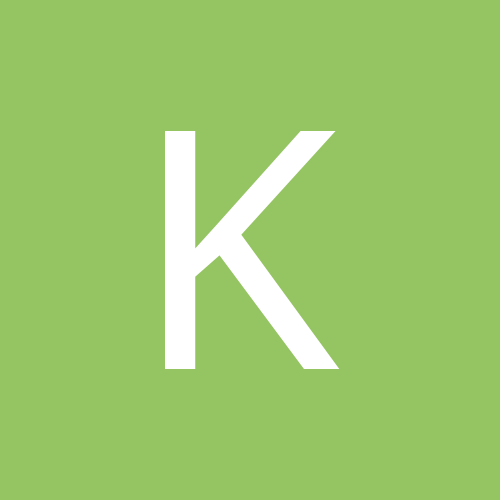
Kristof
Members-
Content Count
72 -
Joined
-
Last visited
Content Type
Profiles
Forums
Gallery
Everything posted by Kristof
-
Help!! Magnet cutting, machine hard to calibrate
Kristof posted a topic in TITAN 2 Series Vinyl Cutter Discussions
Hello, I received a new Titan 2 - 28" model a few weeks ago for the sole purpose of cutting adhesive-backed 30 mil thick magnet. I have been having trouble, however, trying to calibrate the machine; cuts are not square (start and end points don't match up), and the dimensions are wrong of the cut. Example: 235mm dimensions comes out as 230mm. I'm using Sure Cuts a Lot 4 Pro and have played with the calibration settings to resolve the dimension issues; it works sometimes but is inconsistent from job to job and I am wasting a lot of material by doing this. I've done jobs pulling off of the roll directly AND by pulling some off of the roll manually, so the machine isn't trying to pull from a 70 lb. roll of material. I would like to say that pulling from the roll directly is not good as we can all agree on, but either way it doesn't resolve the issue entirely of the start and end points not lining up when I unroll the material manually before each job. The cut jobs are DXF files generated by Autodesk and I've verified the files are spot on in dimension with multiple programs and they are correct in Sure Cuts a Lot 4 Pro. I'm using a new CleanCut Roland Metal 60º carbide blade and am using the stated offset that was on the box of the blade, 0.5mm. http://cleancutblade.mybigcommerce.com/roland-60-metal/ I have overcut set to 0.5mm. My cut speed is 12mm/s and pressure at 300grams. Do I need an infeed and outfeed table that is horizontal with the cutting bar plane? At this point I'm stressed out and not sure what to do as this was a big investment to eliminate manual cutting, material waste and so I could offer custom shapes for my customers. I appreciate the help and hope I don't have to return the machine. I've attached a pic below showing two magnets that show the non-square cut issue of the start and end points not lining up. -
Help!! Magnet cutting, machine hard to calibrate
Kristof replied to Kristof's topic in TITAN 2 Series Vinyl Cutter Discussions
Thank you, Sue! I am grateful for the wealth of posts that were posted here. I guess I have not explained myself well enough and people don't understand what I want -
Help!! Magnet cutting, machine hard to calibrate
Kristof replied to Kristof's topic in TITAN 2 Series Vinyl Cutter Discussions
You asked the question on why the material would be wasted, so I replied to you with a legitimate answer.. -
Help!! Magnet cutting, machine hard to calibrate
Kristof replied to Kristof's topic in TITAN 2 Series Vinyl Cutter Discussions
Probably because I don't want to cut the roll into sheets. -
Help!! Magnet cutting, machine hard to calibrate
Kristof replied to Kristof's topic in TITAN 2 Series Vinyl Cutter Discussions
It's called nesting in the industry; you can get more parts out of a single 24 ft long sheet than two 12 ft sheets, depending on the part dimensions. If one part is 13 feet, neither sheet can be used and is why longer steel lengths are better (in this case magnet material). -
Help!! Magnet cutting, machine hard to calibrate
Kristof replied to Kristof's topic in TITAN 2 Series Vinyl Cutter Discussions
The material is expensive and the market doesn't support high margins, just the way it is. Honestly, the prefeed would function perfectly if there were more than two options. If it didn't have that ramp up acceleration it wouldn't trigger an error. I don't see why I can't set the pre feed speed in cm/s. -
Help!! Magnet cutting, machine hard to calibrate
Kristof replied to Kristof's topic in TITAN 2 Series Vinyl Cutter Discussions
Cutting the material would be a waste of material for subsequent jobs where the cut line would've fell onto the next sheet, which potentially means a loss of 280mm of material. The roll should be kept continuous to not waste the material. The geometry of the stock rollers is what causes unnecessary drag, they should be mounted up higher so that the material feeds in a planar manner and not angular (the departure angle of the roll). Most jobs would be 560x560 but I may occasionally get odd ball jobs from customers that need to be 560mm in width by whatever length they specify. Hopefully you understand.. -
Help!! Magnet cutting, machine hard to calibrate
Kristof replied to Kristof's topic in TITAN 2 Series Vinyl Cutter Discussions
I was thinking that more rollers increases the amount of pulling weight and more traction, since the weight is spread out over four rollers. I already built a smooth melamine outfeed table that mounts to the stand and that turned out nice. -
Help!! Magnet cutting, machine hard to calibrate
Kristof replied to Kristof's topic in TITAN 2 Series Vinyl Cutter Discussions
I wanted to utilize that feature. I think the media stocker rollers are mounted too low and the pulling angle creates drag that it has to fight against. -
Help!! Magnet cutting, machine hard to calibrate
Kristof replied to Kristof's topic in TITAN 2 Series Vinyl Cutter Discussions
WV. Do you think having more push rollers would stop the 'media too heavy' error from occurring when I do the pre feed? The error occurs even with the pre feed speed set to slow. It prefeeds fine at first and then as it accelerates it triggers the error; if there were a way to disable that acceleration/ramp up for pre feeding, that would solve my issue. -
Help!! Magnet cutting, machine hard to calibrate
Kristof replied to Kristof's topic in TITAN 2 Series Vinyl Cutter Discussions
There's not a dealer close to me. -
Help!! Magnet cutting, machine hard to calibrate
Kristof replied to Kristof's topic in TITAN 2 Series Vinyl Cutter Discussions
The force is currently at 28 and speed set at 2cm/s with acceleration of 1. I've heard that people have problems with tangential emulation, so I didn't think to try using that since it's not a true tangential machine and I don't think I need it, as all of the DXFs have corner radii and never sharp transition corners. I uninstalled Sure Cuts a Lot since it's not very good software and am using the Illustrator and Cutting Master 4 plugin, which allows me to use the plotter on the network and is awesome! DXFs seem to be importing fine into Illustrator for now. Still curious on how the push roller assemblies are installed so I can keep that as a last resort. None of the service manuals mention it. -
Help!! Magnet cutting, machine hard to calibrate
Kristof replied to Kristof's topic in TITAN 2 Series Vinyl Cutter Discussions
Would it be a bad idea to cut the magnet with the 3M wax paper side facing the blade? I would get more traction with the grit rollers biting into the magnet material, but the swiveling blade may 'gum up' as it cuts through the 3M acrylic adhesive? Just wondering. Thanks for your input! -
Help!! Magnet cutting, machine hard to calibrate
Kristof replied to Kristof's topic in TITAN 2 Series Vinyl Cutter Discussions
The Graphtec service manual for the FC8000 doesn't even show how to change out the push roller assemblies. -
Help!! Magnet cutting, machine hard to calibrate
Kristof replied to Kristof's topic in TITAN 2 Series Vinyl Cutter Discussions
I'm having trouble locating the post where someone installed the extra rollers; I could've swore I found it on other forum before while doing my initial research of plotters. -
Help!! Magnet cutting, machine hard to calibrate
Kristof replied to Kristof's topic in TITAN 2 Series Vinyl Cutter Discussions
Does it look hard to install/take off the rollers? The square bar looks like it runs through both sides of the machine and it looks like it needs to be taken out. -
Help!! Magnet cutting, machine hard to calibrate
Kristof replied to Kristof's topic in TITAN 2 Series Vinyl Cutter Discussions
Is it pretty easy to install extra push rollers? I have a mechanical background. -
Help!! Magnet cutting, machine hard to calibrate
Kristof replied to Kristof's topic in TITAN 2 Series Vinyl Cutter Discussions
I think I might benefit from installing two additional pinch rollers in the middle; $255 each though. -
Help!! Magnet cutting, machine hard to calibrate
Kristof replied to Kristof's topic in TITAN 2 Series Vinyl Cutter Discussions
I tried the pre feed setting as well, and it causes the machine to report 'media too heavy' even if setting it on the Slow feed setting. -
Help!! Magnet cutting, machine hard to calibrate
Kristof replied to Kristof's topic in TITAN 2 Series Vinyl Cutter Discussions
I guess it does work correctly depending on what you're doing. The blade goes up 5mm (as I want) at the end of a cut job. If the blade is down when powering up the machine and then jogging, it won't go up though, which is what I'd like. -
Help!! Magnet cutting, machine hard to calibrate
Kristof replied to Kristof's topic in TITAN 2 Series Vinyl Cutter Discussions
So, I set the blade up height setting to 5mm to prevent dragging, but the blade doesnt go up to this setting before I jog, which can cause some faint scratches on the media. I'm guessing there's not a setting to keep the blade always up in this 'parked' position until I initiate a cut job. -
Help!! Magnet cutting, machine hard to calibrate
Kristof replied to Kristof's topic in TITAN 2 Series Vinyl Cutter Discussions
Does it put all the pre feed material in the media basket? The magnet would stick to itself. -
Help!! Magnet cutting, machine hard to calibrate
Kristof replied to Kristof's topic in TITAN 2 Series Vinyl Cutter Discussions
I think I lost traction because I didn't pull enough off of the roll accidentally. Is there an external roller stand available to where I can mount on the wall high up and pull off let's say 7 ft (height of wall) at a time? -
Help!! Magnet cutting, machine hard to calibrate
Kristof replied to Kristof's topic in TITAN 2 Series Vinyl Cutter Discussions
Unfortunately, with the liner side facing down, I lost traction and the second pass was way off from the first one -
Help!! Magnet cutting, machine hard to calibrate
Kristof replied to Kristof's topic in TITAN 2 Series Vinyl Cutter Discussions
When I change the calibration to the following screenshot, the 50mm square turns out correct.